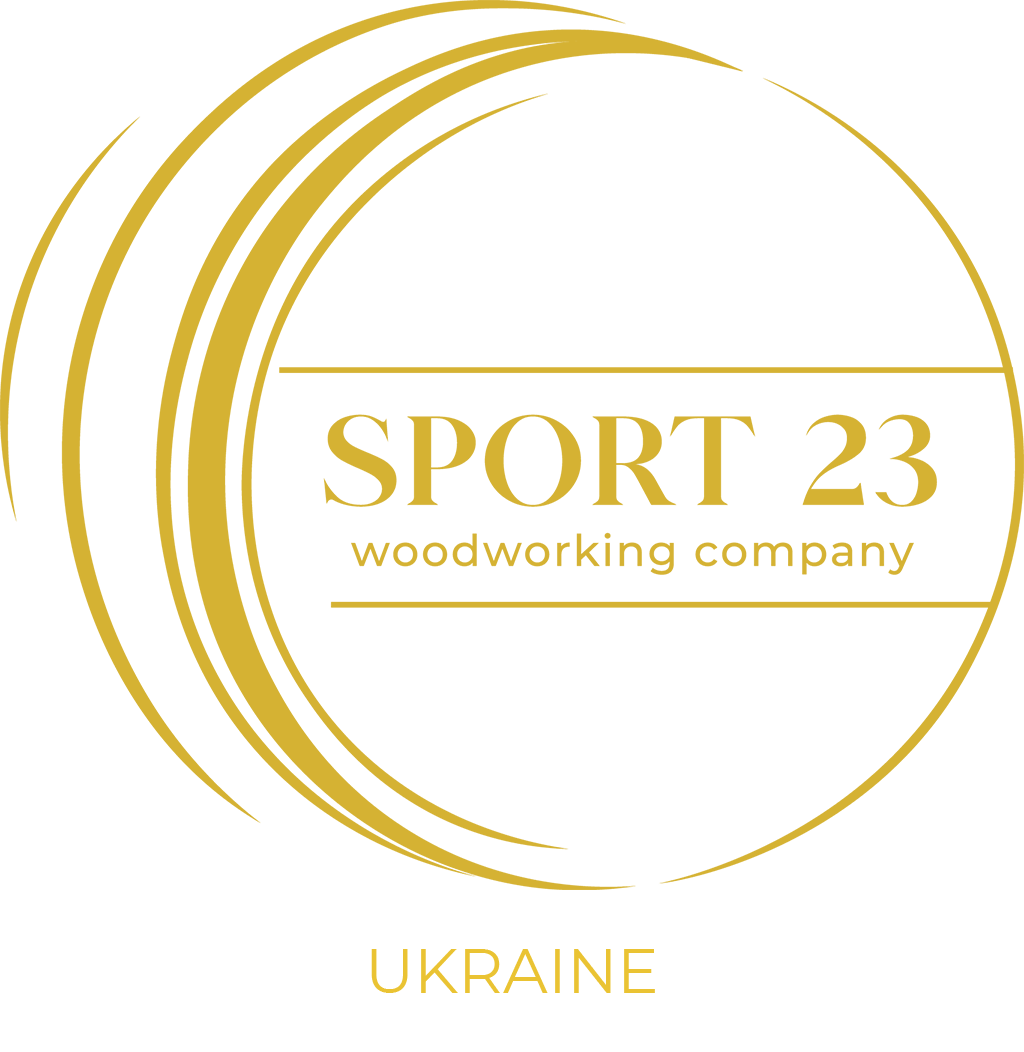
O n l y t i m e d e t e r m i n e s q u a l i t y
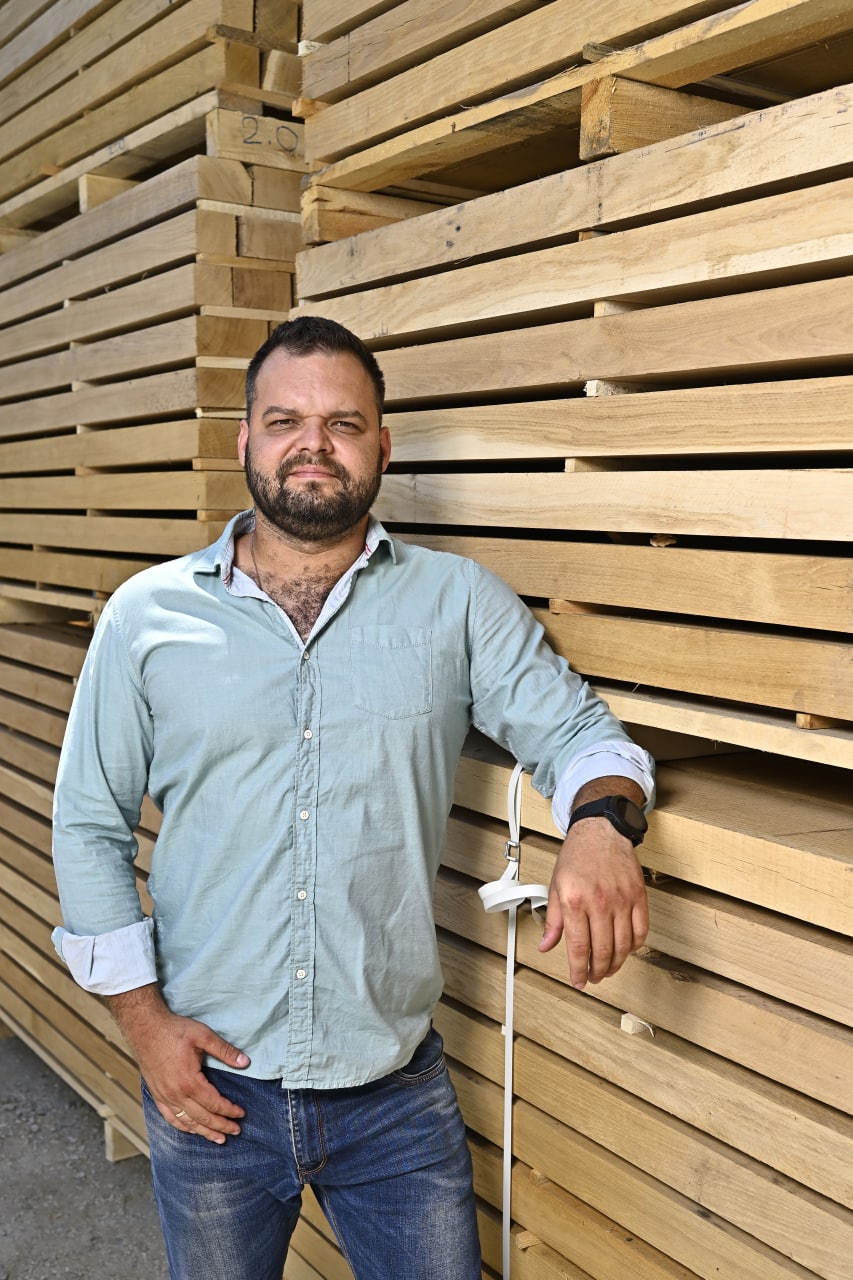
A b o u t u s
The woodworking company “SPORT 23” LLC was founded in 2009 in Popilna, Zhytomyr region. The immediate proximity to the raw material base and the best quality of oak among all of Ukraine were the main arguments in choosing a place for production. All these years, the company has been moving forward without looking back, without stopping in front of difficulties, but also without forgetting where it all started. Over the years, the entire production team has learned that there is nothing more valuable than quality that is determined by time. Our entire team works as one mechanism to ensure that, even after many years, customers get pleasure from cooperation and from a product that, even after years, evokes only positive emotions.
Once, after trying to work with oak wood, it became clear that this wood has its own character and should be treated with respect. Oak has a solid body and a tough character. Skillfully cutting, drying, creating a product and properly preserving oak is not an easy task. Oak does not forgive frivolity and lack of neatness. Careful use of wood is the key to the future of a woodworking enterprise. That is why our company always tries to keep up with modern woodworking technologies, using equipment that makes it possible to save such valuable wood as much as possible.
This is especially important in the production of lamellas, where we fight for every 0.1 mm of thickness. A properly selected technological line makes it possible to compete with other enterprises.
In the production of stave, the most important factor is the quality selection of wood directly from the plot in the forest. Here it is important that all the wood has an even layer, that the annual rings are dense, that the trunk is even, and that the core is in the center of the log. For the production of stave, we use no more than 7 meters of trunk from the comel. Only the best logs end up in stave production.
Working for quality, we are clearly aware that the time will come when quality will start working for us. We strive to pass on our experience to the next generation, as well as the culture of production and respect for wood. We do not live in one day, we care about forests and the future of the woodworking industry of Ukraine.
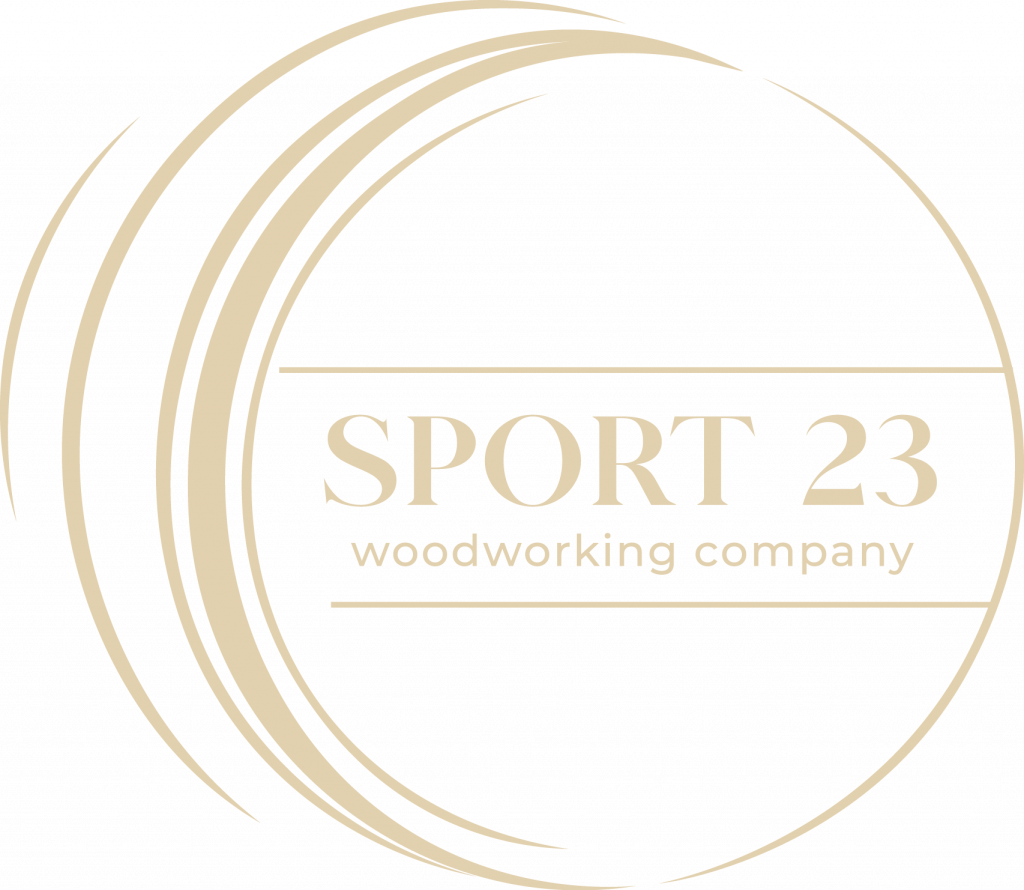
experience
M a n u f a c t u r i n g
Production was established in 2009. For many years, the company has been engaged in the deep processing of oak and the production of stave and lamellas from it. It has a completely closed cycle. The main product is stave, which account for 60% of the processing volume, of which more than 80% is stave for large wine barrels with a capacity of 500 to 5000 liters and only 20% are classic stave.
The lamella takes up 40% of the processing. The company’s specialty is the production of large-sized lamellas, up to 6 m long. and up to 500 mm wide.
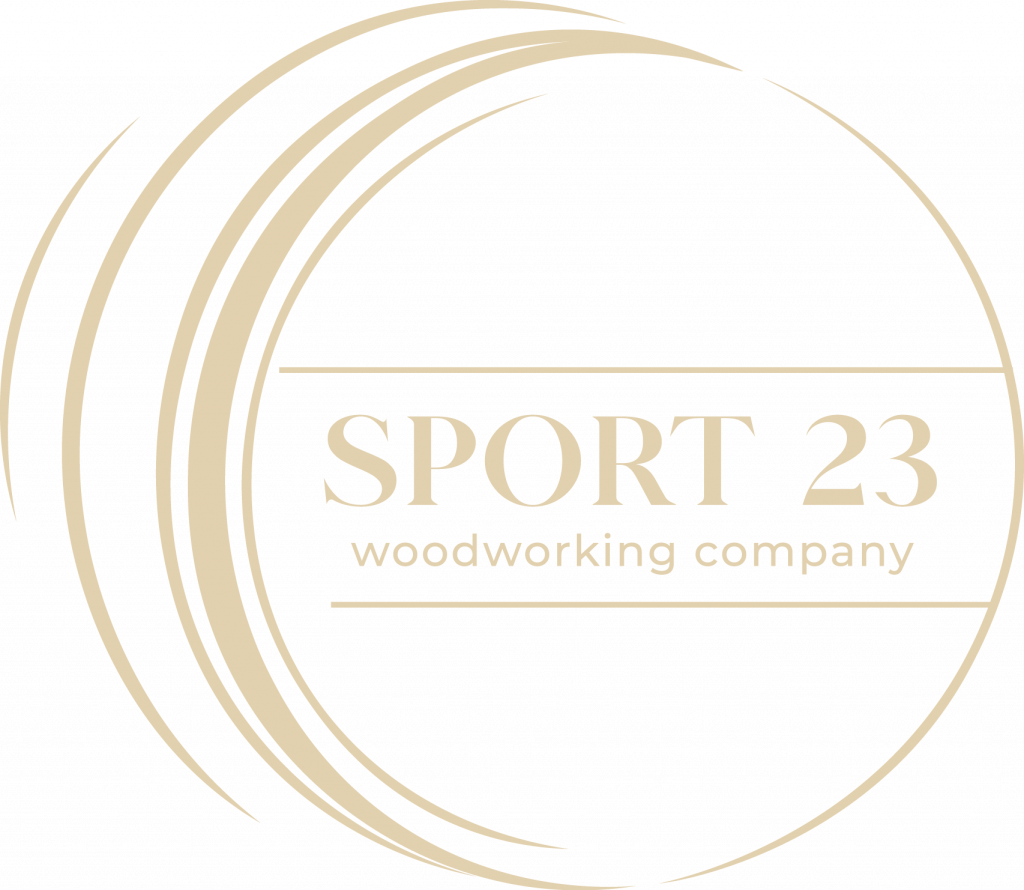
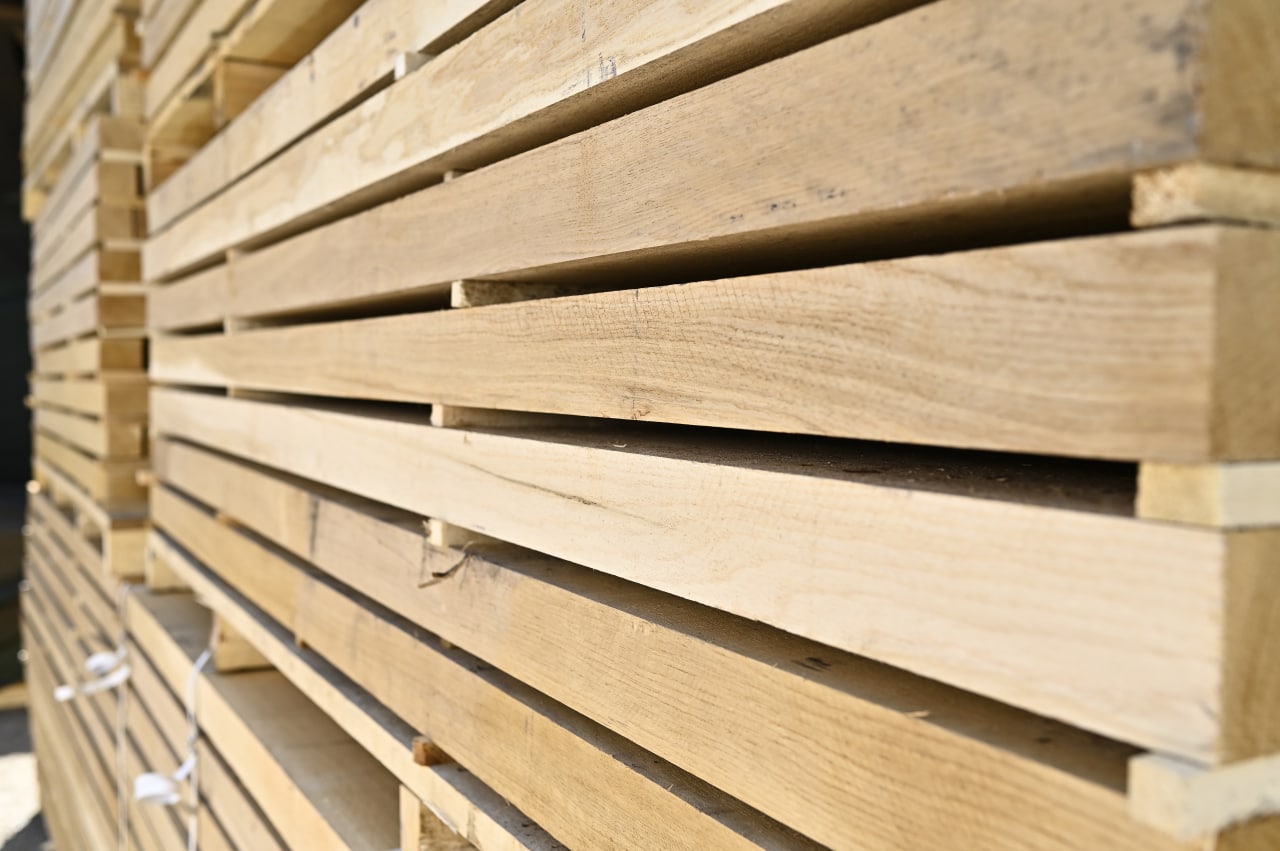
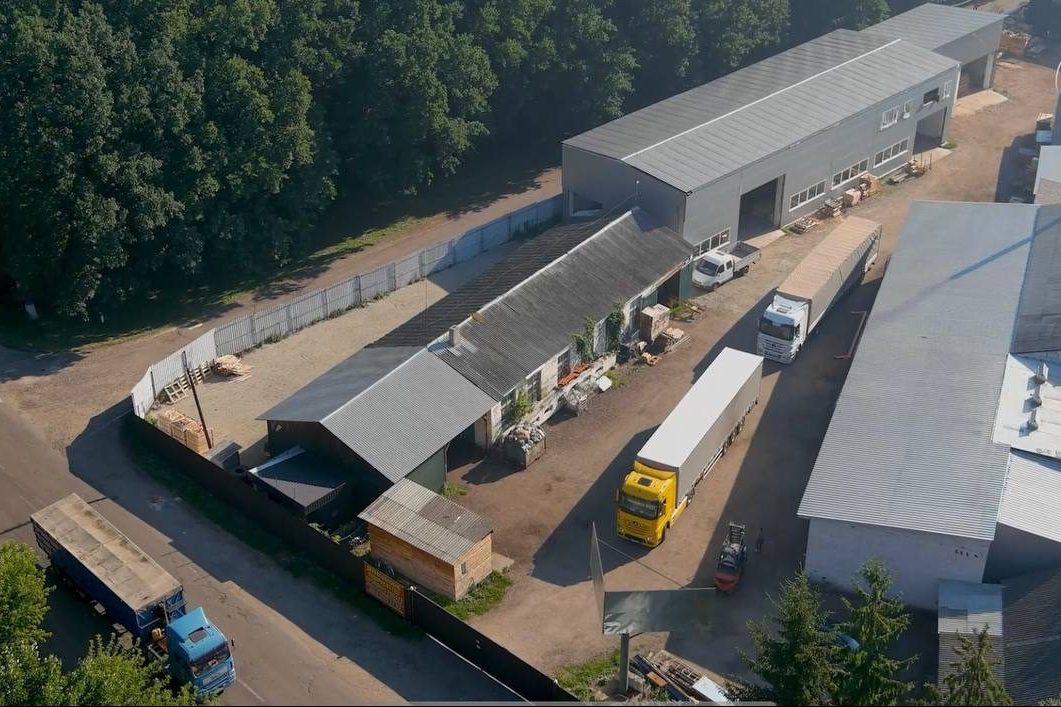
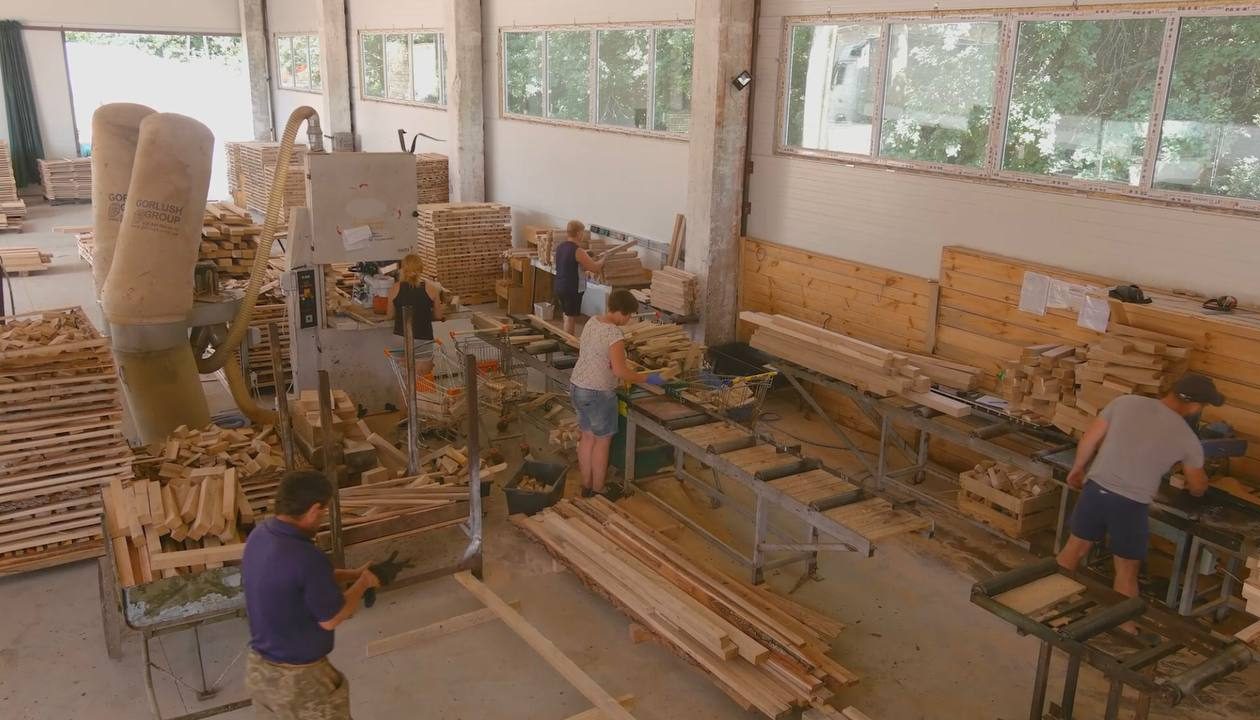
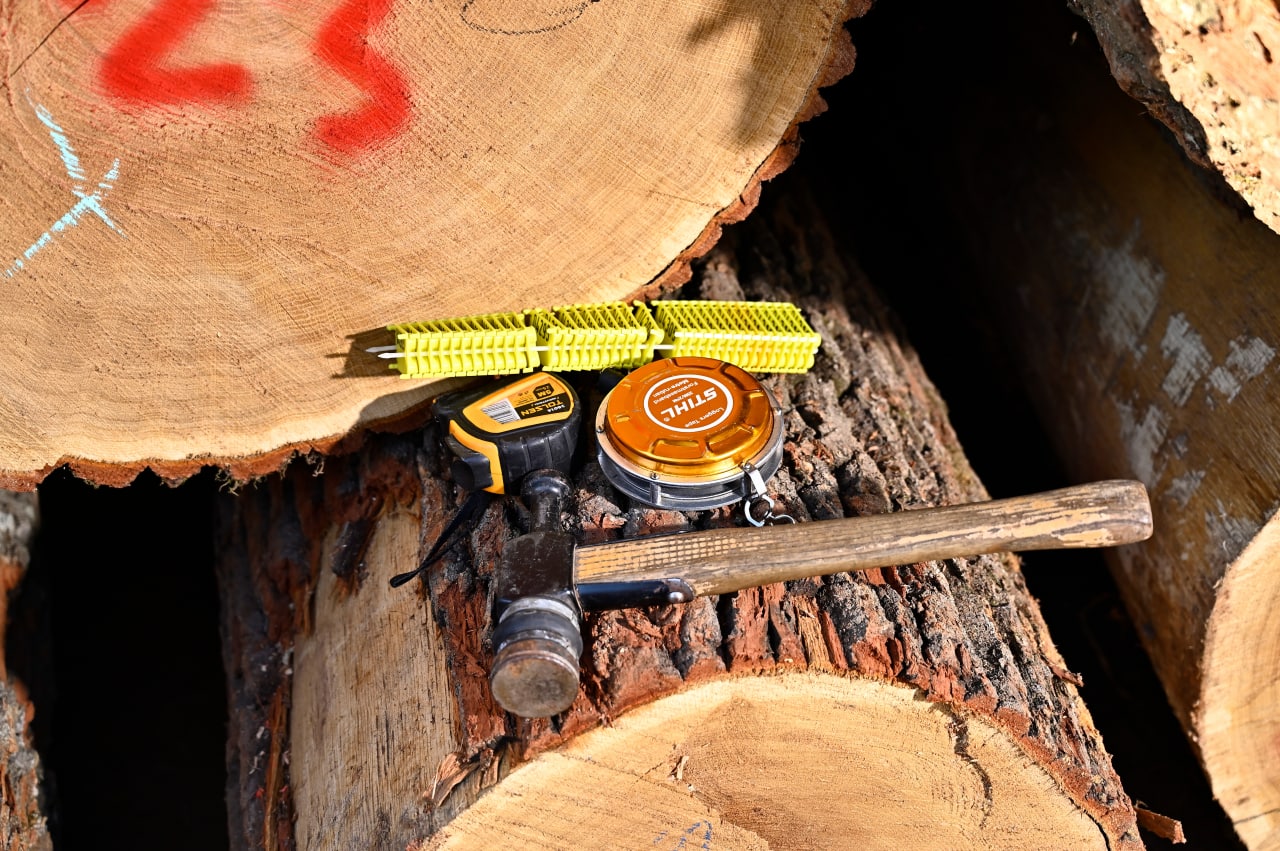
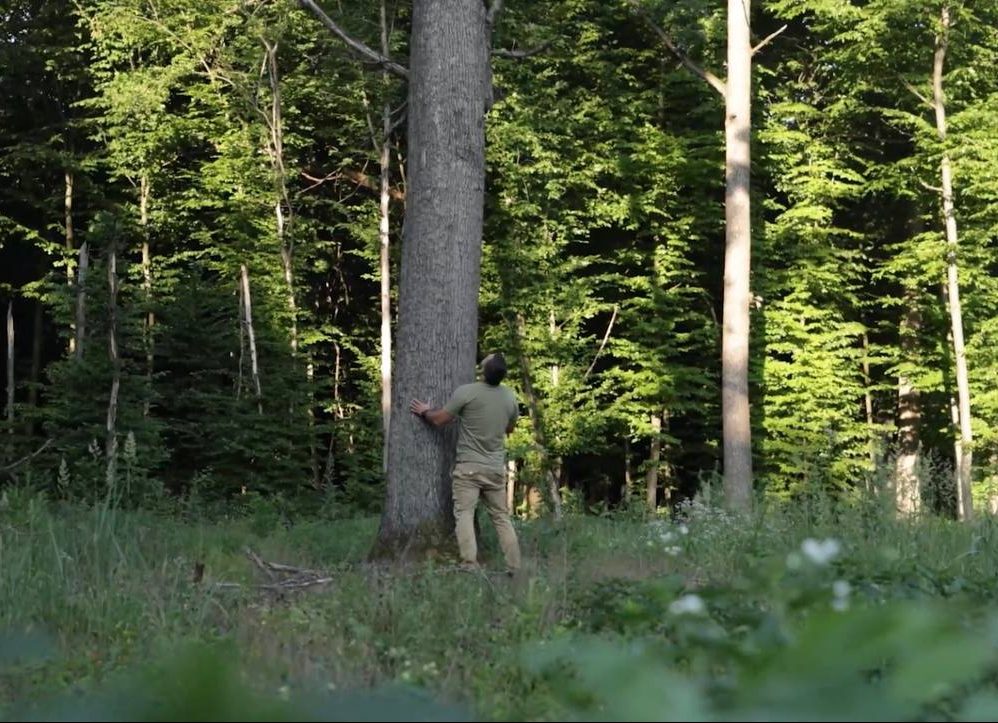
One of the most important processes is the selection of wood according to the technological requirements of the enterprise. For staving, wood must meet many parameters, such as: evenness of grain, density of annual rings, solid part exactly in the center, diameter of the upper section at least 36 cm, absence of peeling cracks. Damage by insects, dry matter and inner sapwood are strictly prohibited. In addition, the logs must be cut lengthwise according to the size of the rivet or its multiple.
All logs that have a diameter of less than 36 cm, or have twisted fibers or other defects, are used at our company for the production of lamellas. Such a combination of two different products at one enterprise greatly facilitates the selection of forest products and allows more rational processing of wood.
manufacturing
S e l e c t i o n o f r a w m a t e r i a l s
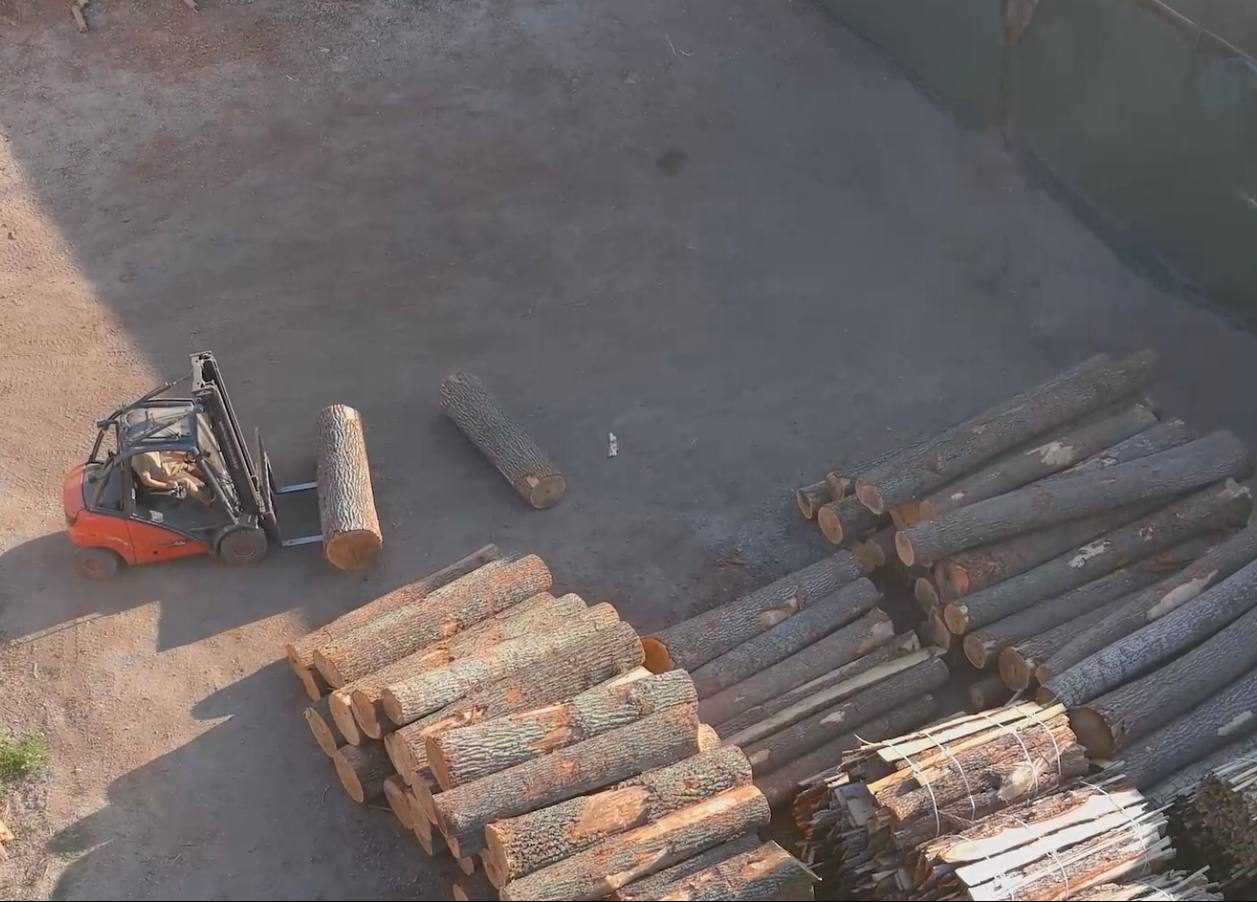
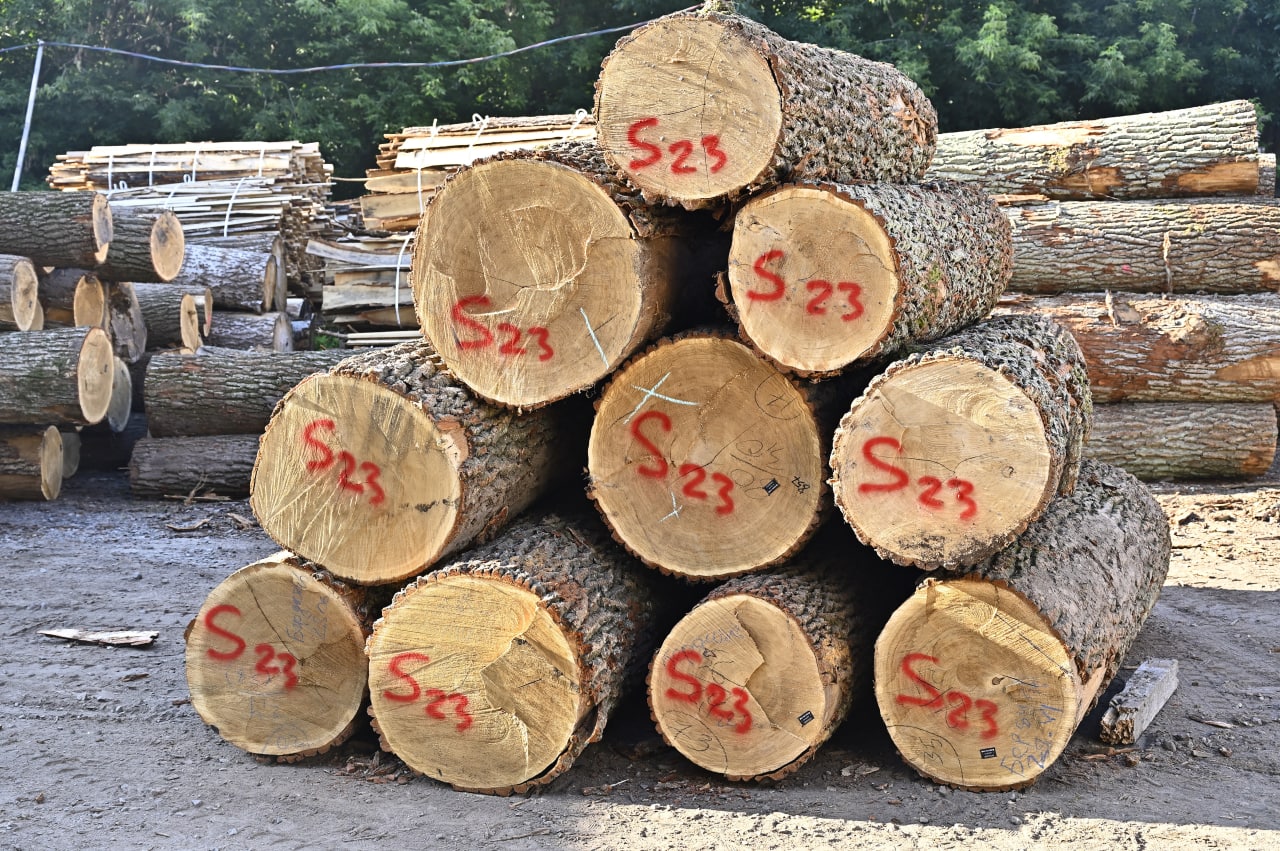
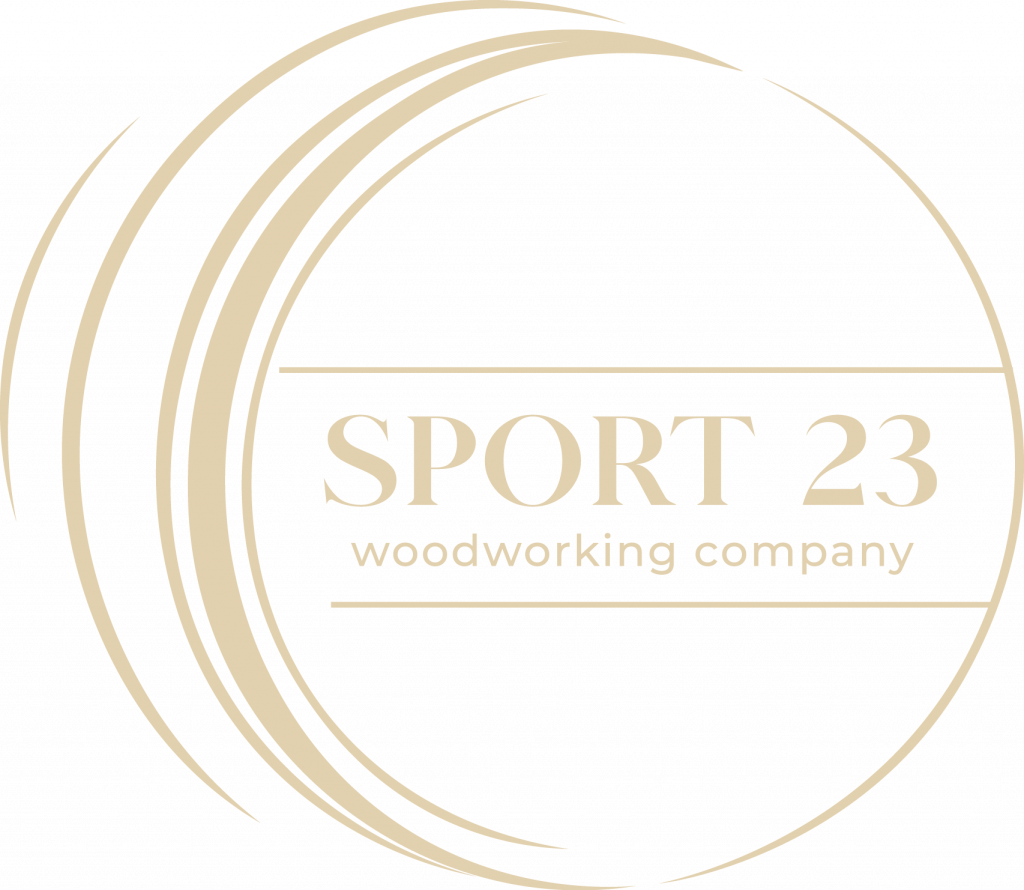
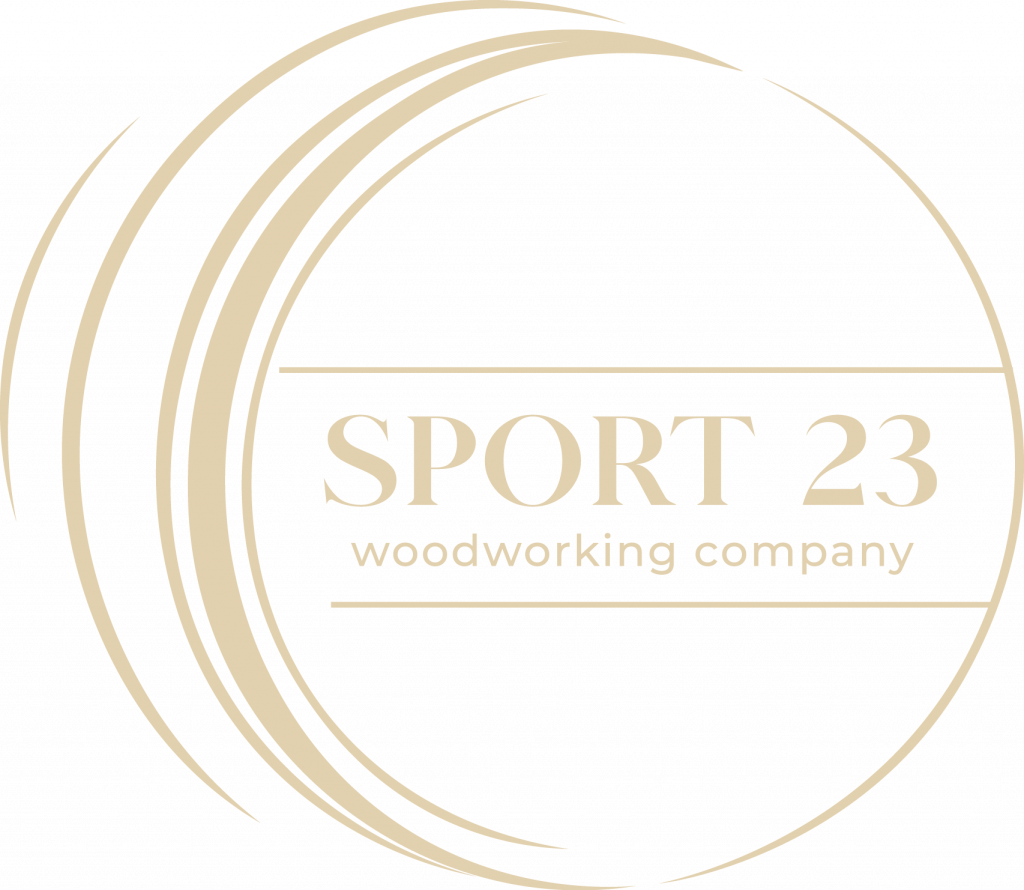
manufacturing
R a w s a w i n g s h o p
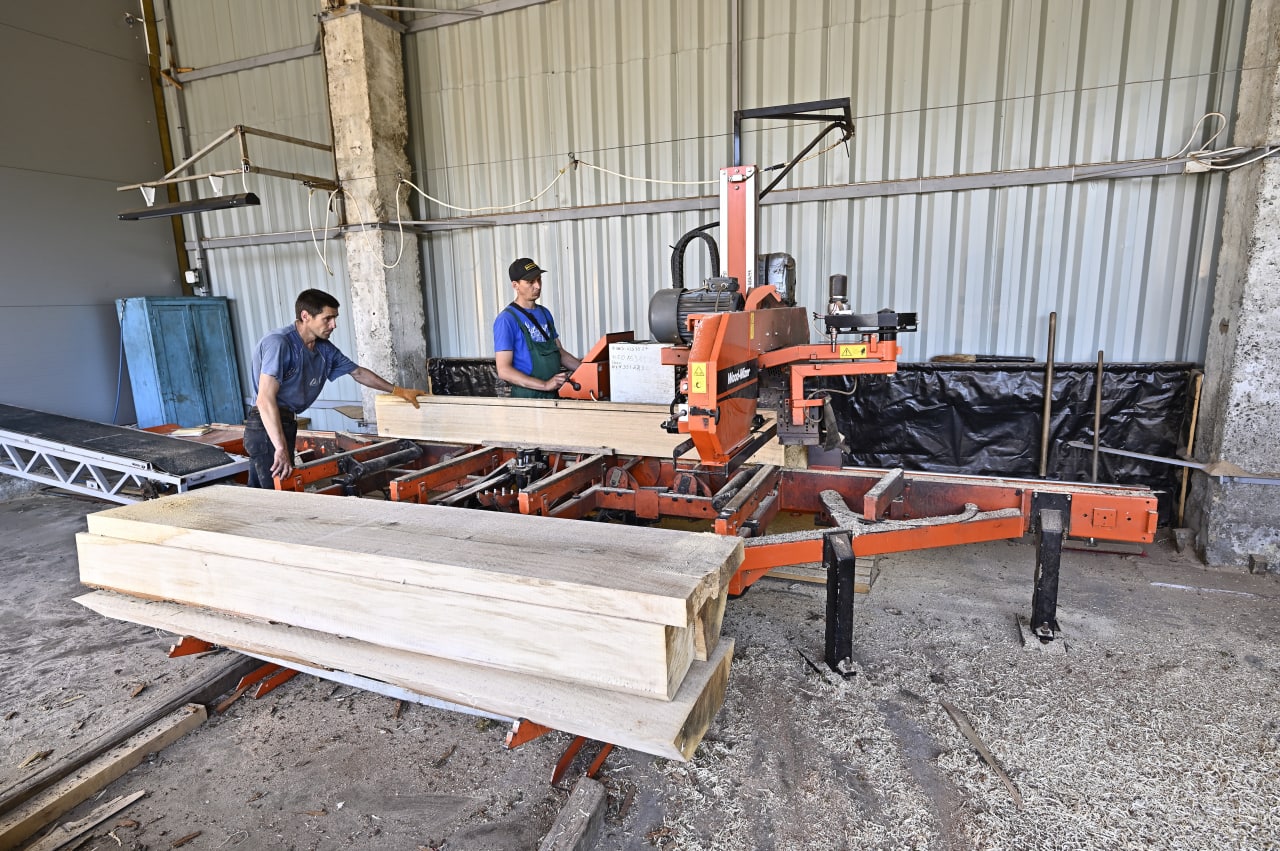
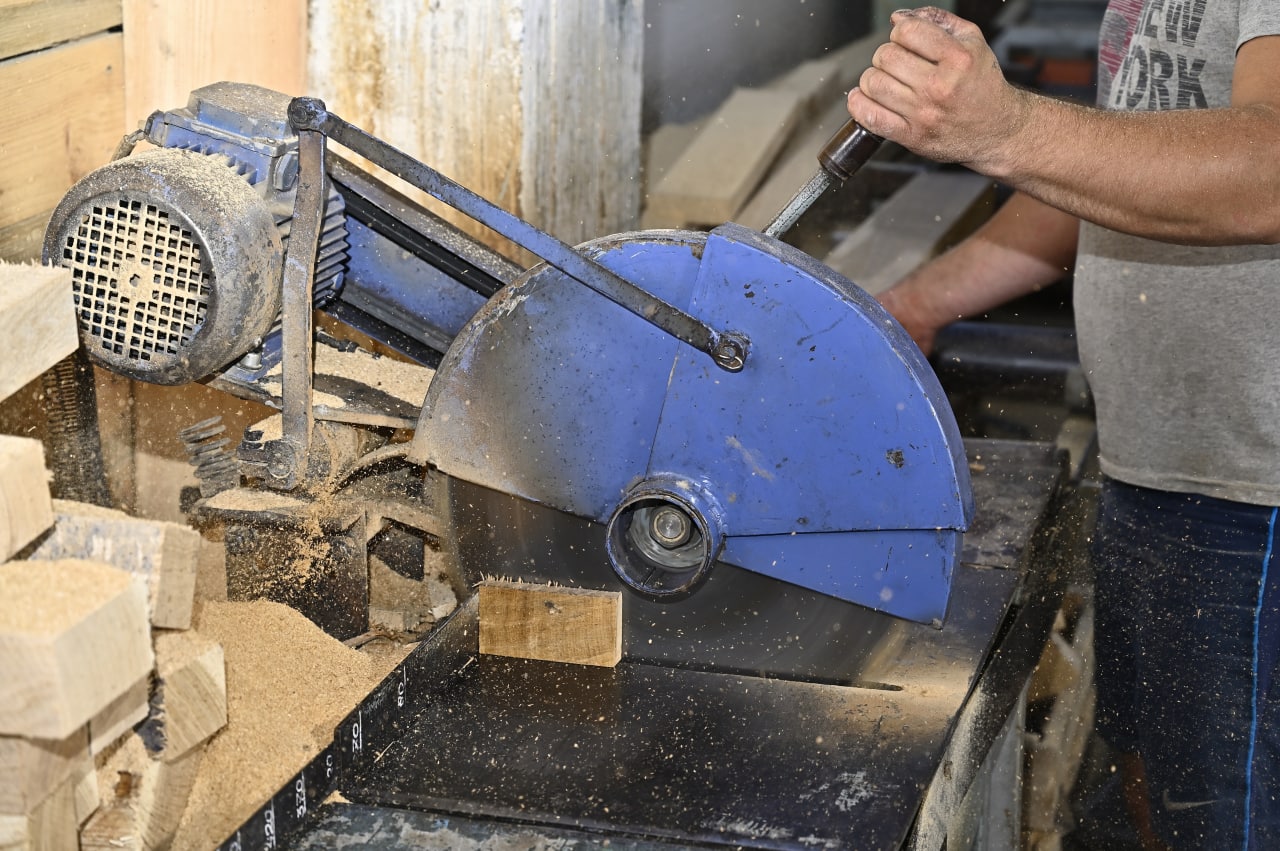
The raw sawing shop includes the following stages of production:
1. Saw logs lengthwise on a frame band saw
2. Cutting the board along the width on the edge-cutting machine
3. Ending along the length
4. Finalization of the workpiece on vertical belt machines
5. Paraffin treatment (only for lamella)
6. Sorting and stacking products on pallets.

According to the classic French technology, we manufacture stave in the following sizes:
in length 90, 95, 100, 110, 115 cm
27, 32 mm thick
Production processes:
Ending of logs lengthwise
Splitting logs into segments
Radial sawing into dies of the required thickness
Cutting across the width
Facing to a given length
Stacking in pallets
manufacturing
P u n c h e d r i v e t s h o p
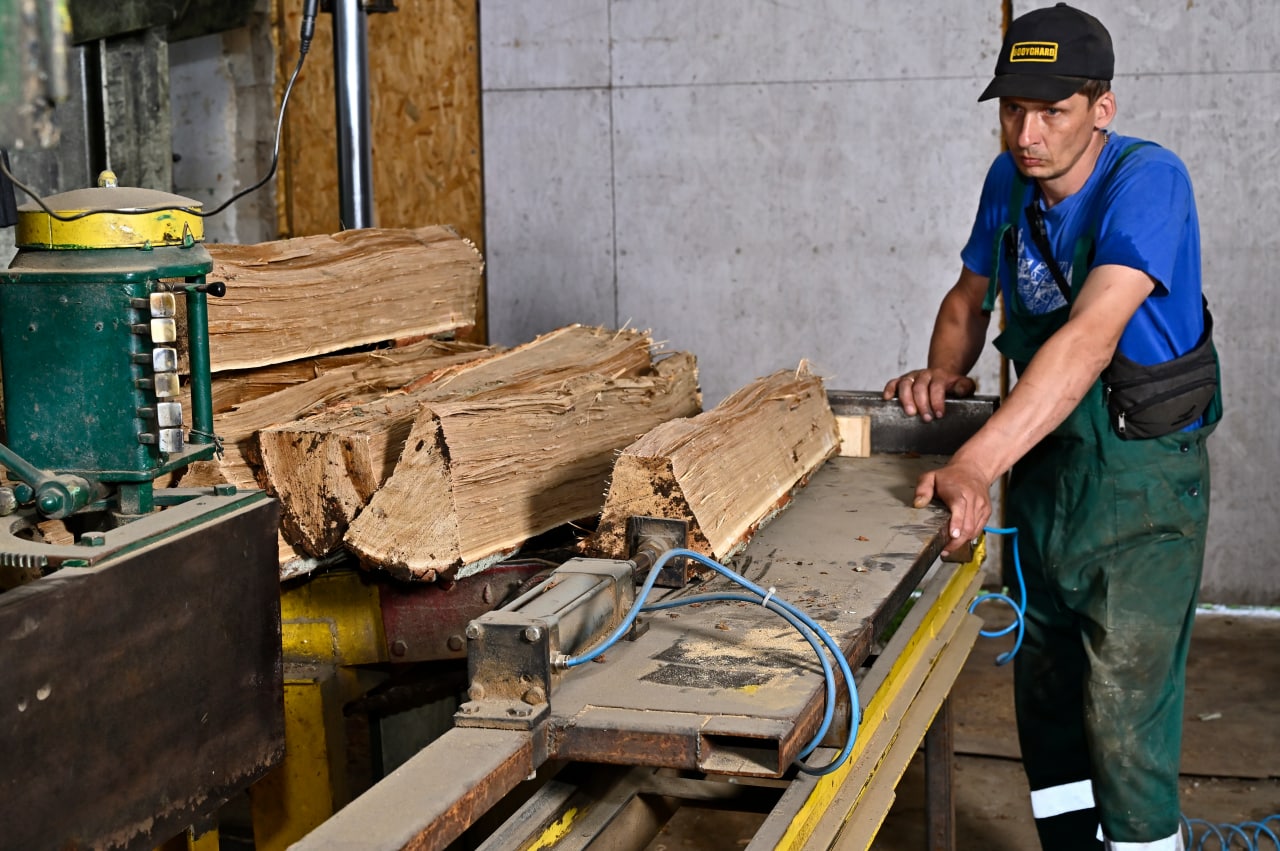
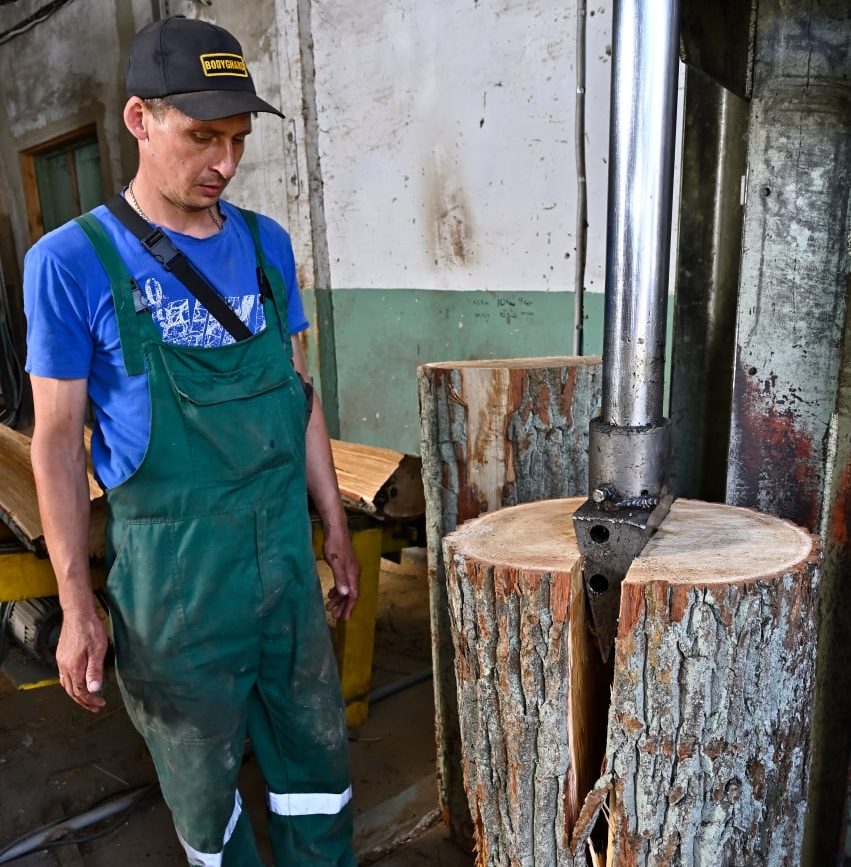
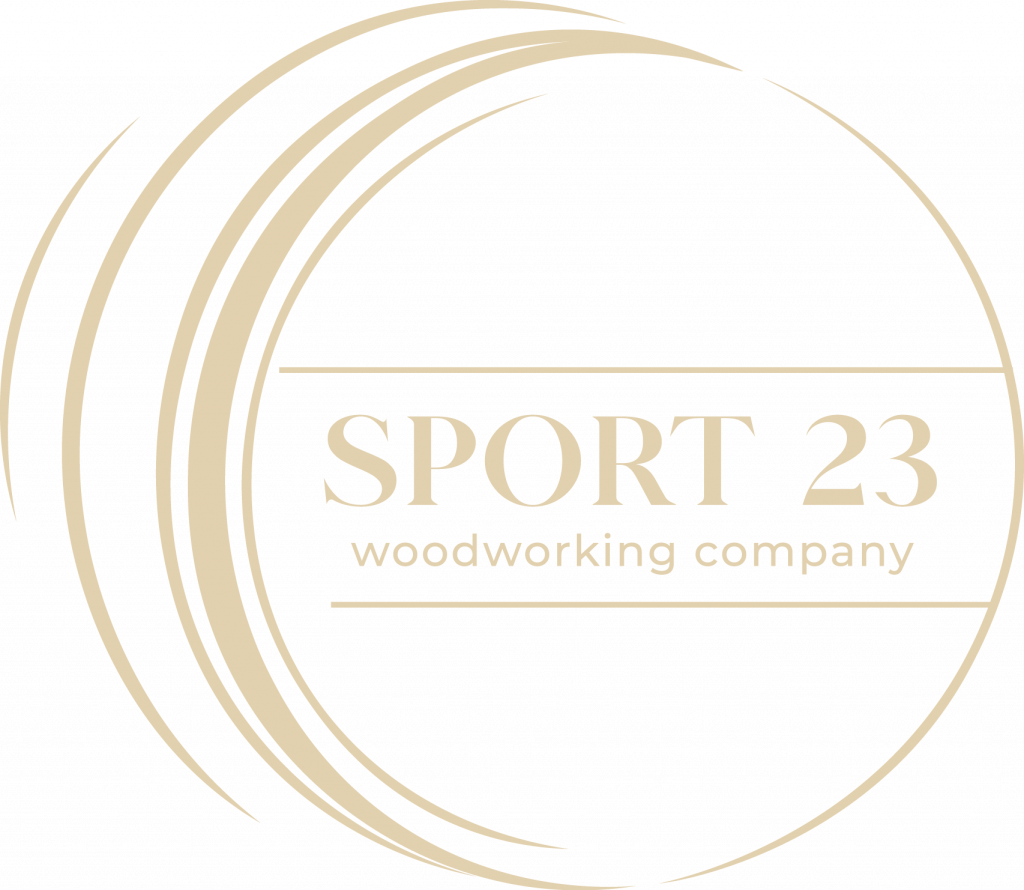
manufacturing
L a m i n a t e w o r k s h o p
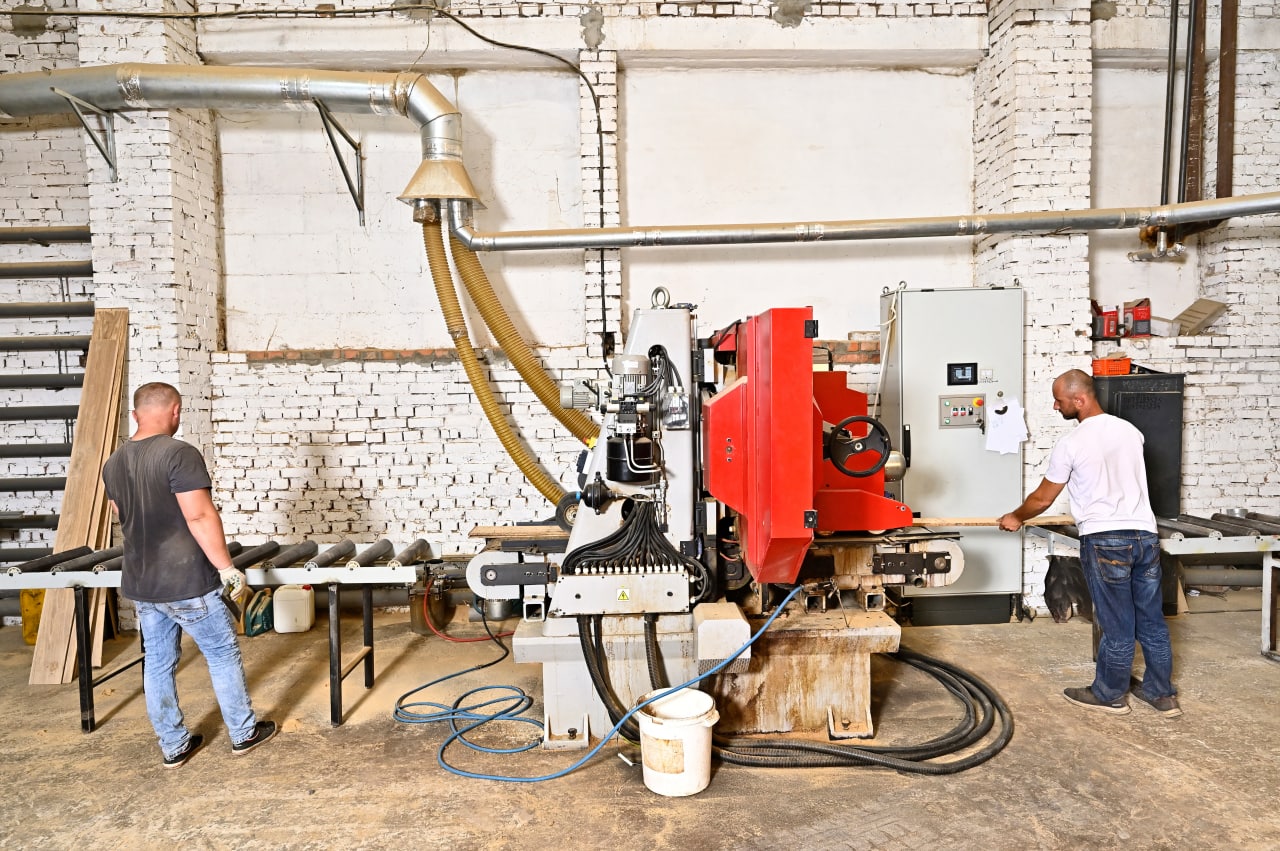
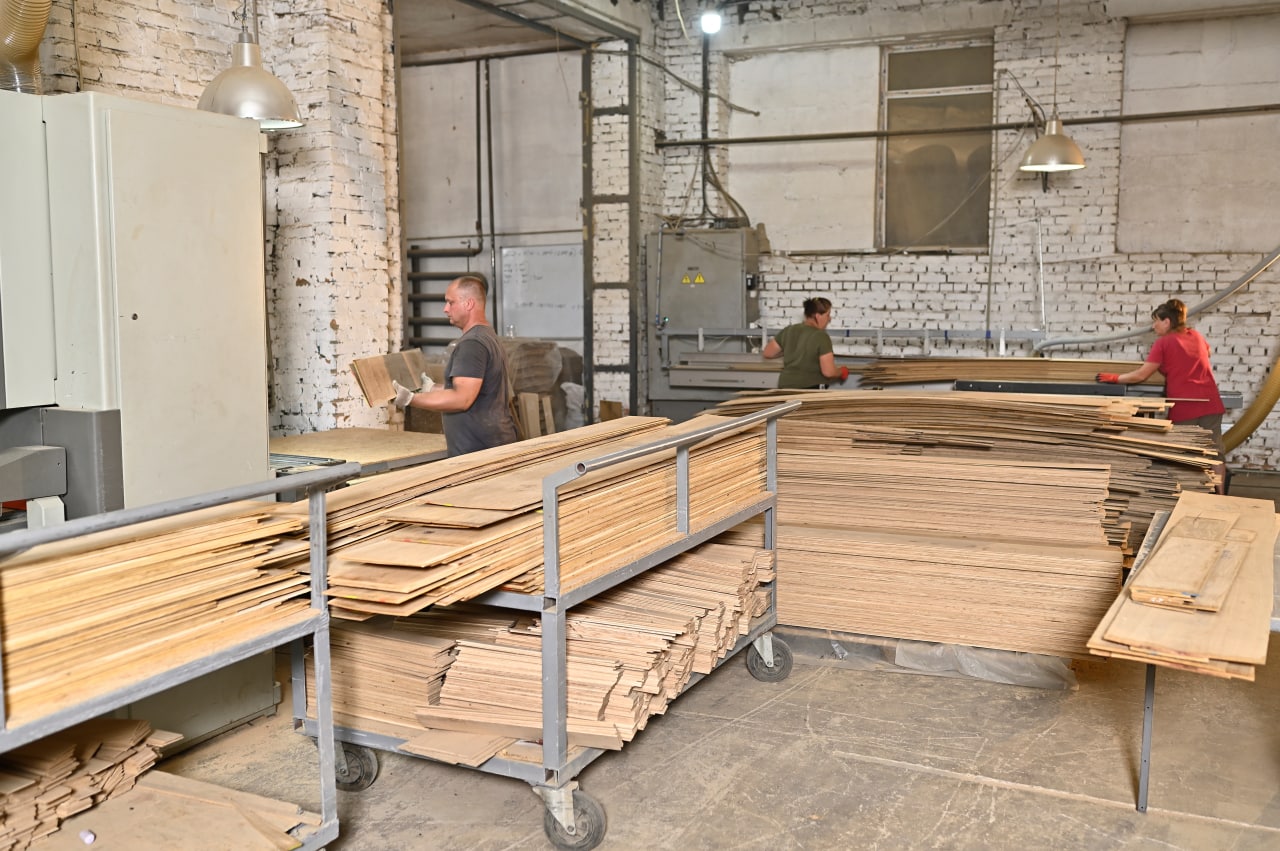
Lamella production is a technologically complex process that requires ideal geometry, great experience in drying wood, and most importantly, its proper preservation from the stage of board production in the raw sawmill to the stage of sorting and stacking the finished lamella.
The finished lamella has a moisture content of 6-9%, therefore, starting from the processing shop and ending with the composition of the finished products, everything must comply with the established temperature regimes, limited ingress of sunlight, moisture, etc.
We manufacture lamellas using the following technology:
We divide the lamella board into 5 lamellas thanks to ultra-fine sawing on the lamella divider.
Drying the lamella in a press-vacuum dryer
Thickness calibration
Cutting across the width
Ending
Sorting and stacking in pallets
Our technology allows us to produce lamellas in large sizes, up to 500 mm in width and up to 6000 mm in length.
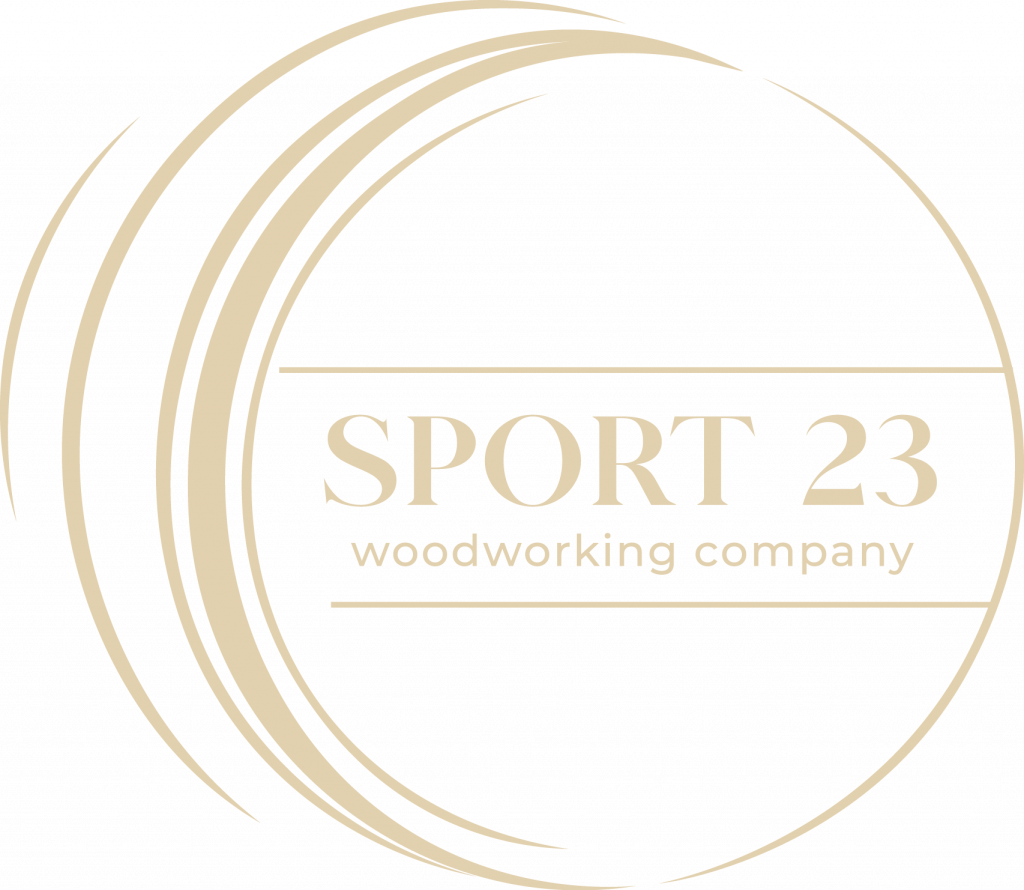
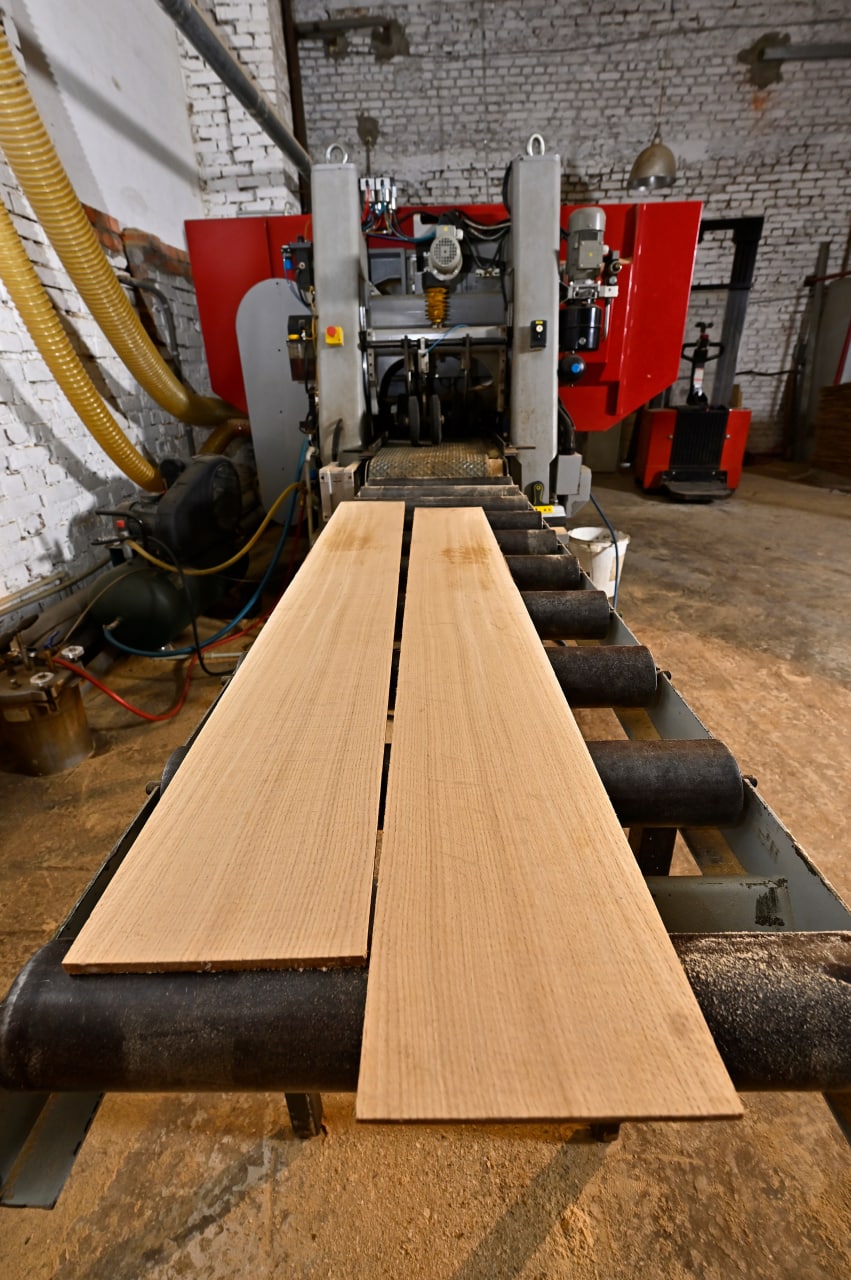
Our company has many years of experience in drying oak wood.
We use the method of convective drying and press-vacuum.
In most cases, the convective drying chamber is used to dry lamella boards with a thickness of 30-55 mm, or blanks for the production of parquet.
The chamber has a volume of 120m3. The whole process is automated. A board with a thickness of 30 mm and an initial humidity of 60% is dried for 35-45 days. Thanks to gentle drying, the board comes out of the chamber flat and without cracks.
Press-vacuum drying is a certain know-how in the process of manufacturing lamellas. This chamber is designed to dry the lamella in a very short time of 13-17 hours, gives maximum flexibility in order fulfillment, allows you to save the lamella after drying without deformation, which allows you to save on the thickness of the raw lamella, and preserves the light, even color of the oak, which, in in turn, affects the grade of the lamella.

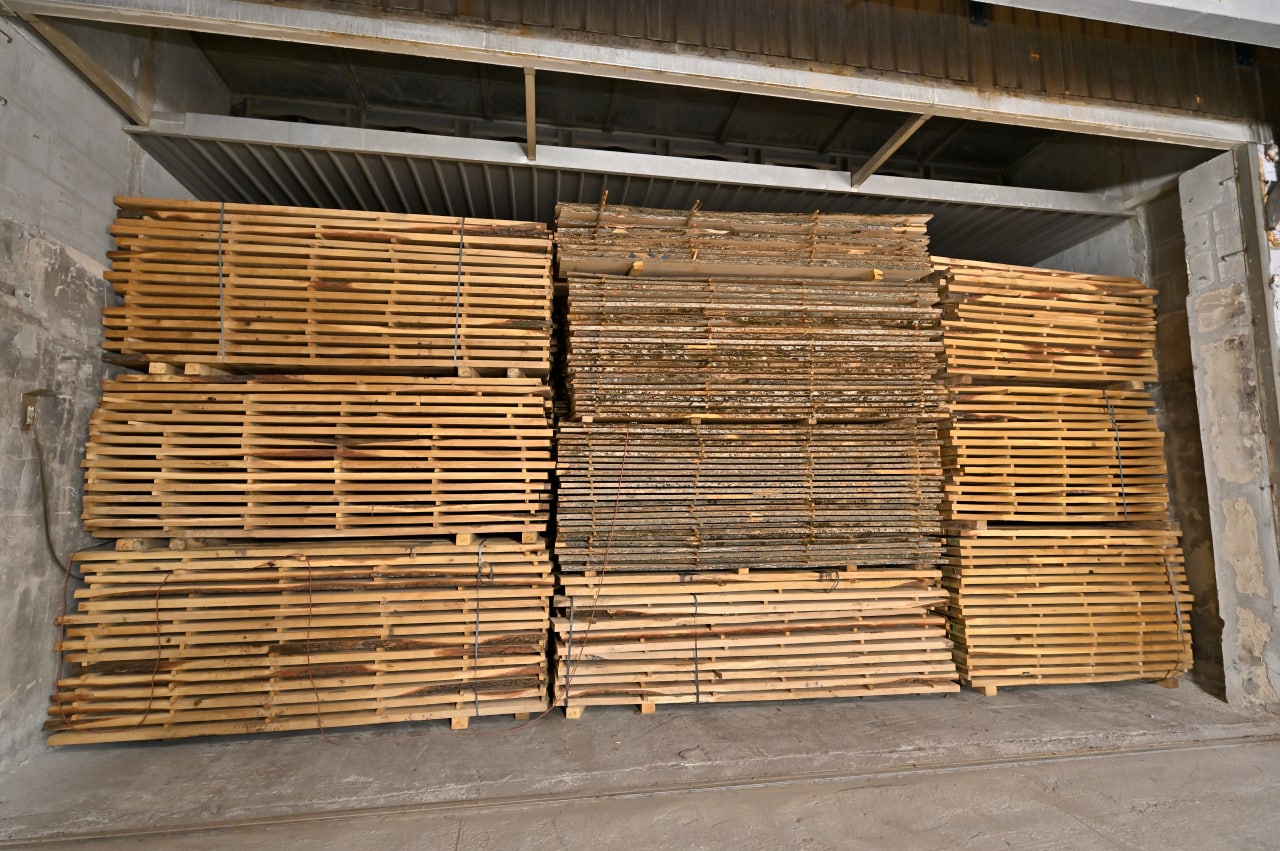
manufacturing
D r y f a r m i n g
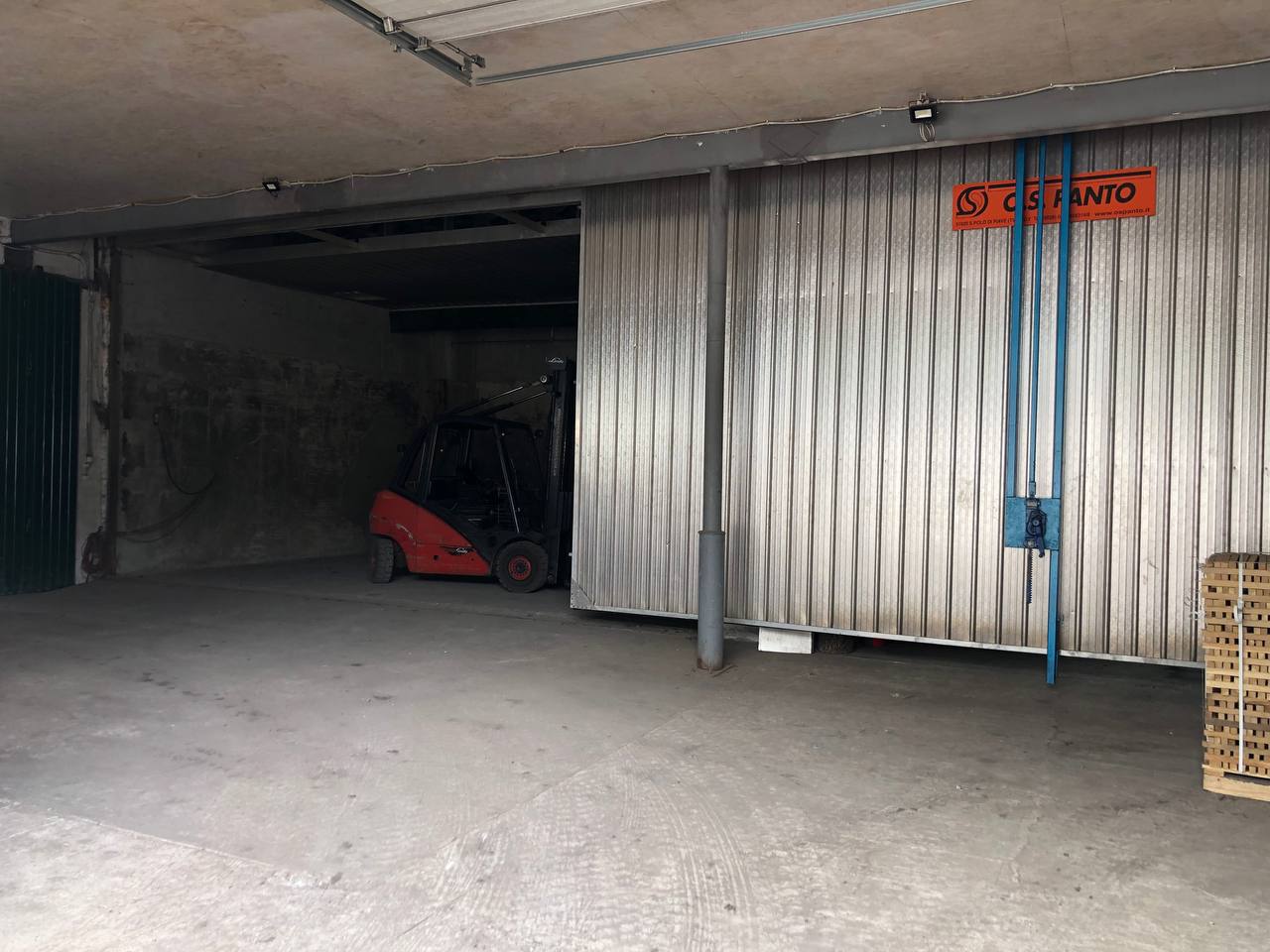
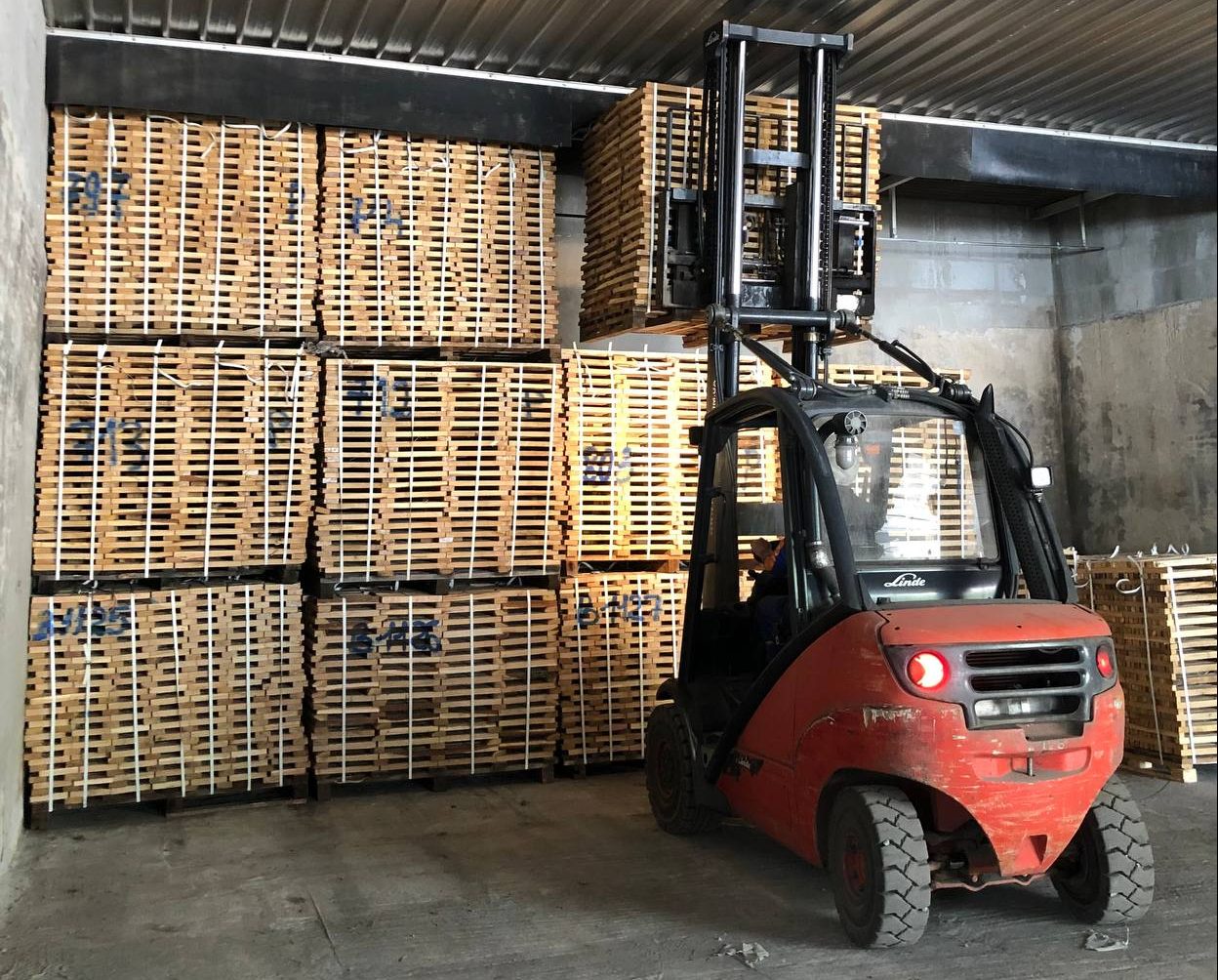
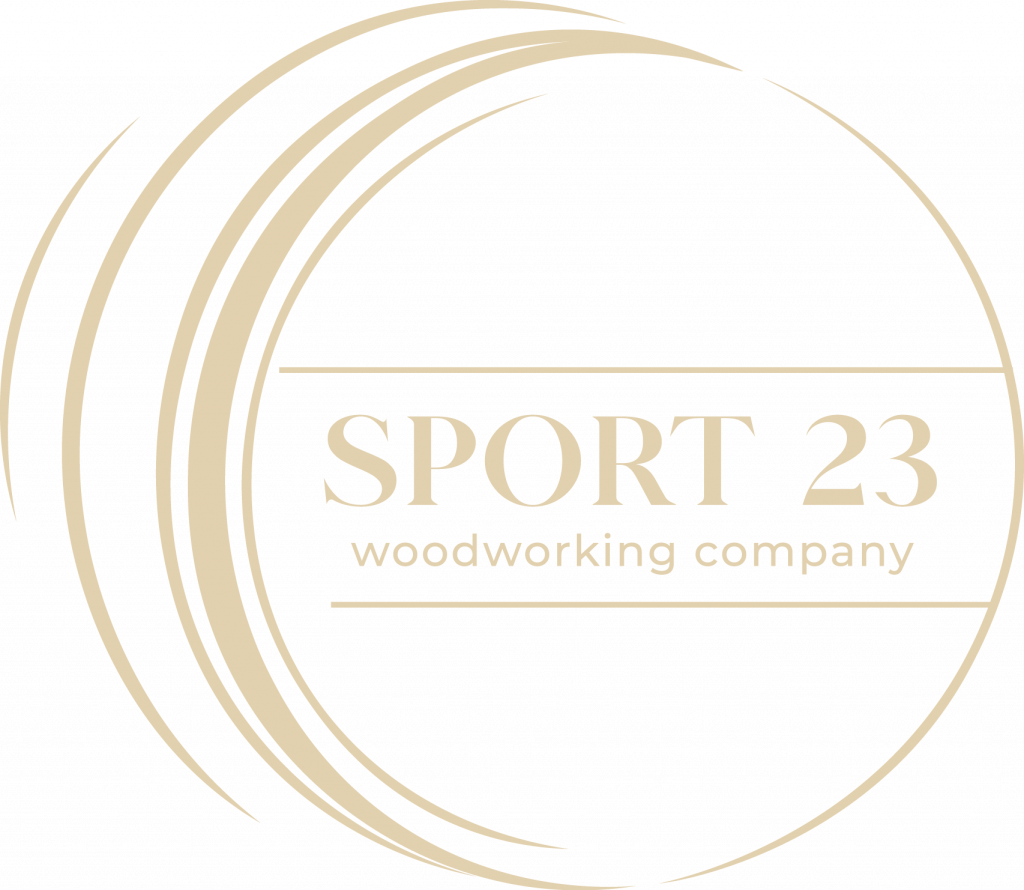
P r o d u c t
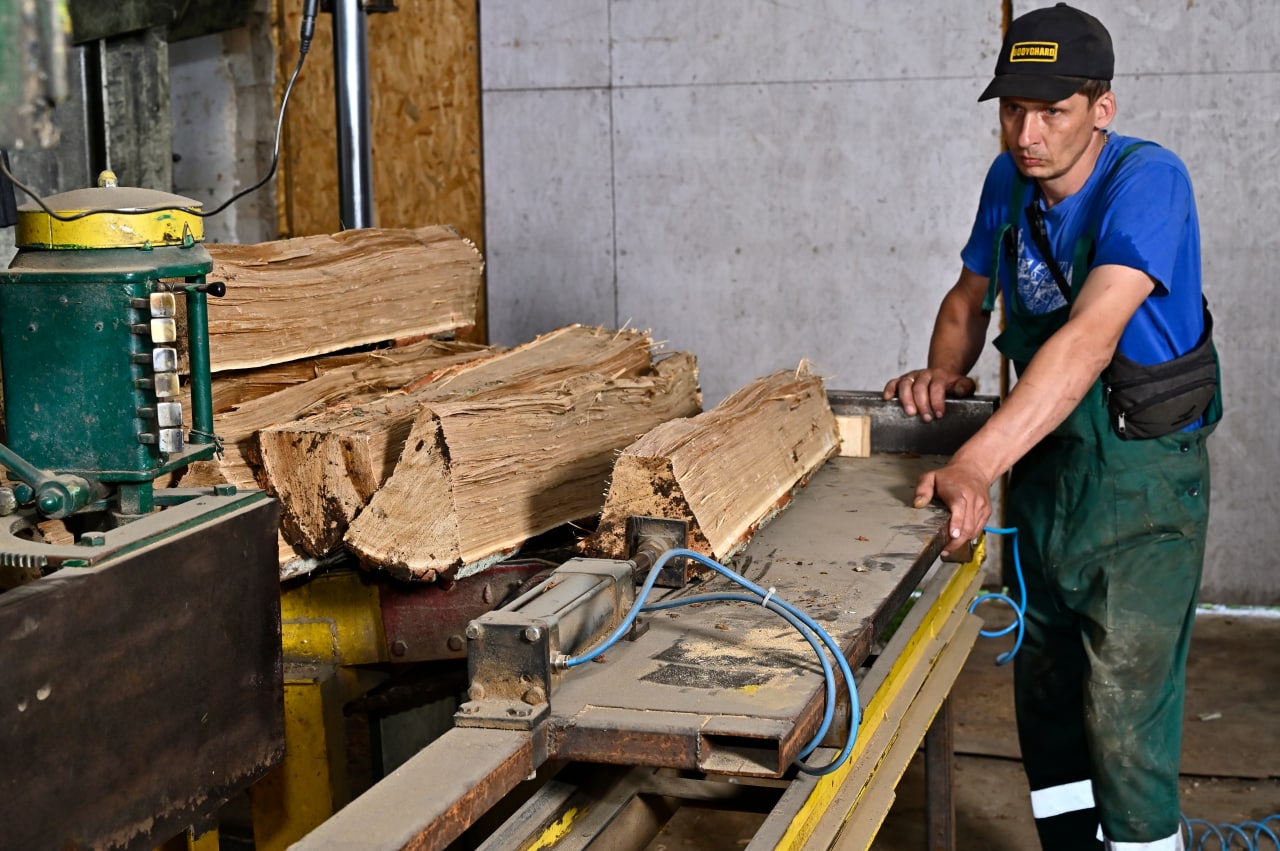
The calculated thickness is 27 mm (+5 mm)
The measuring width is 60-125 mm
The measured length is 900, 950, 1000, 1100, 1150 mm (+40 mm). Basic dimensions.
The measured length is 500, 550, 600, 650, 700, 750, 800 mm (+40 mm). Short sizes.
Proportion in main and short sizes 75% / 25%
The density of annual rings GM 1-2.5 mm GF 2.5-5 mm
Products
T h e r i v e t i s c l a s s i c
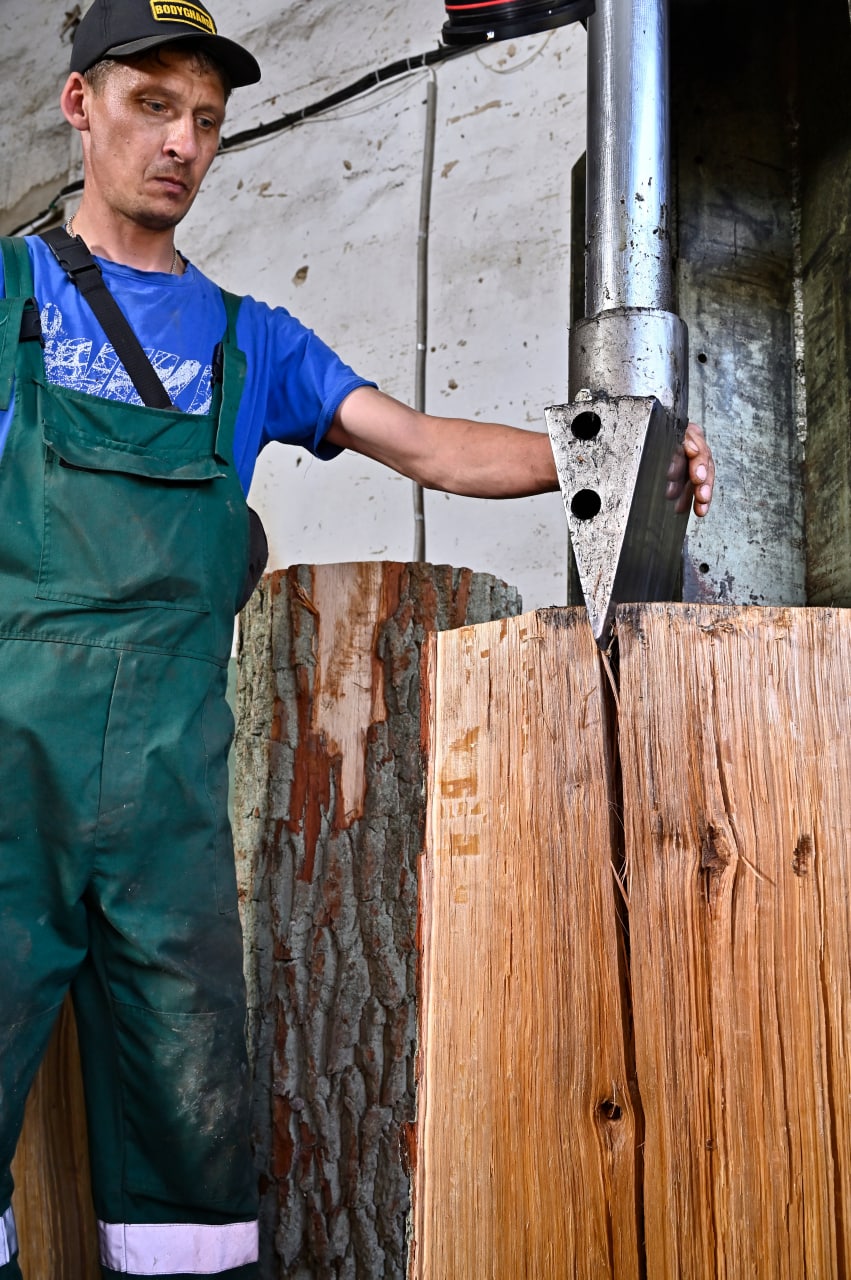
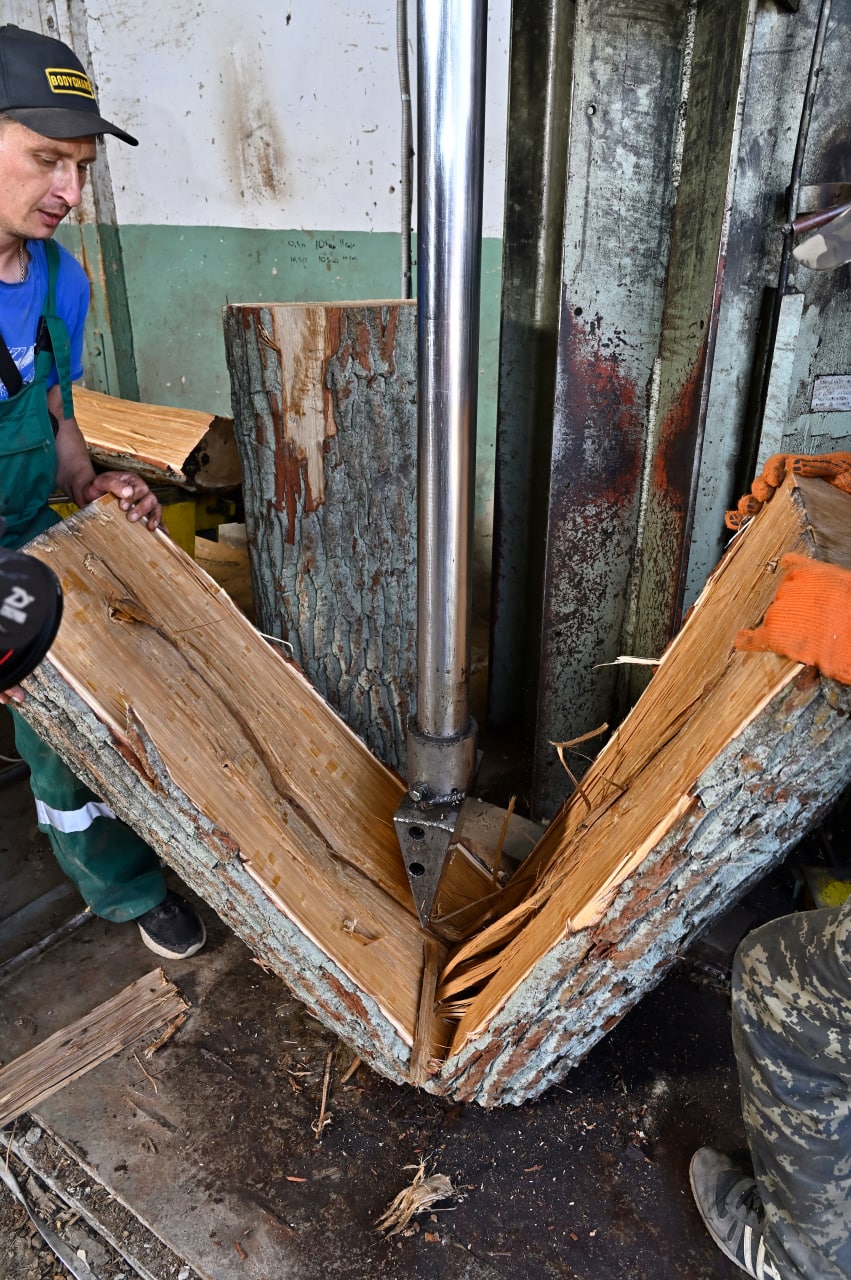
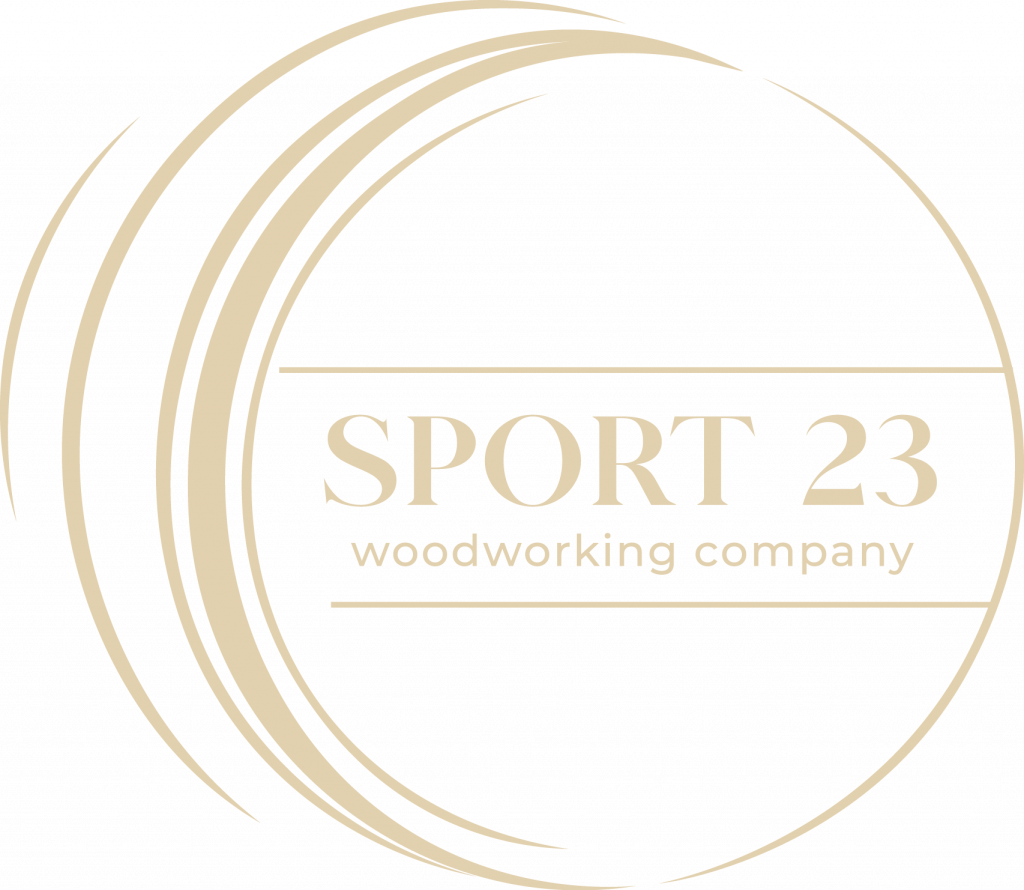
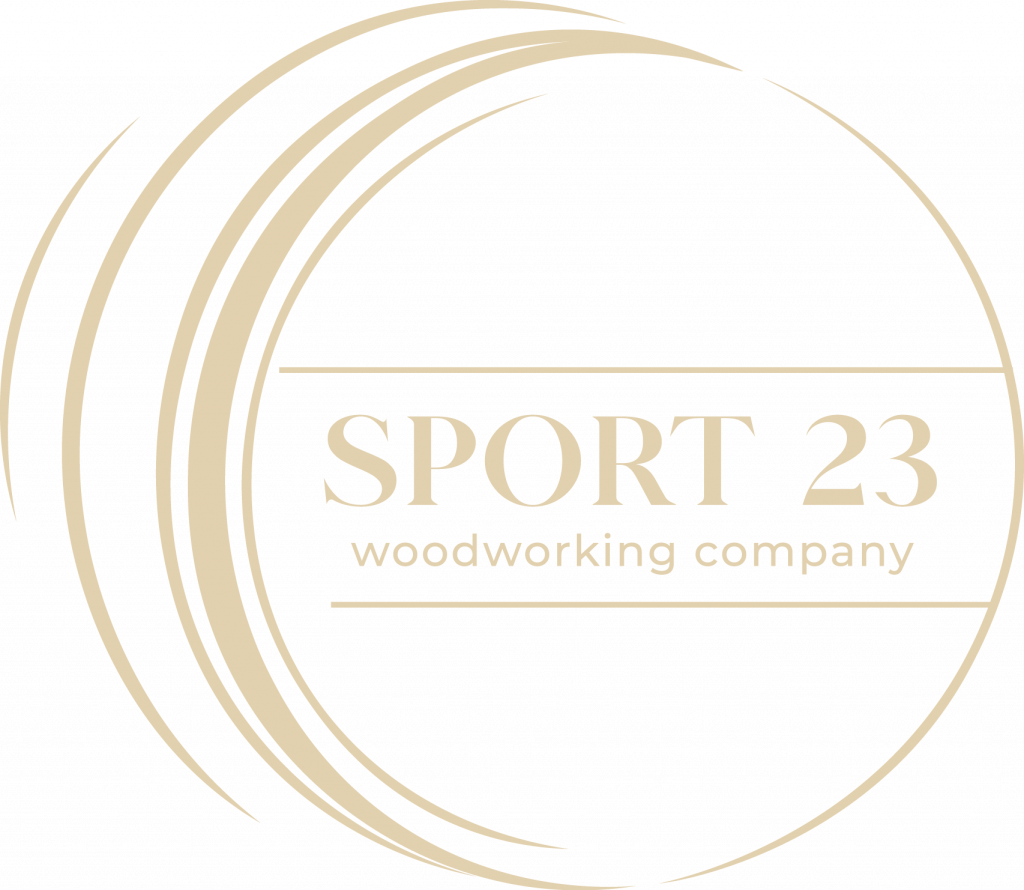
Products
R i v e t o f l a r g e s i z e s
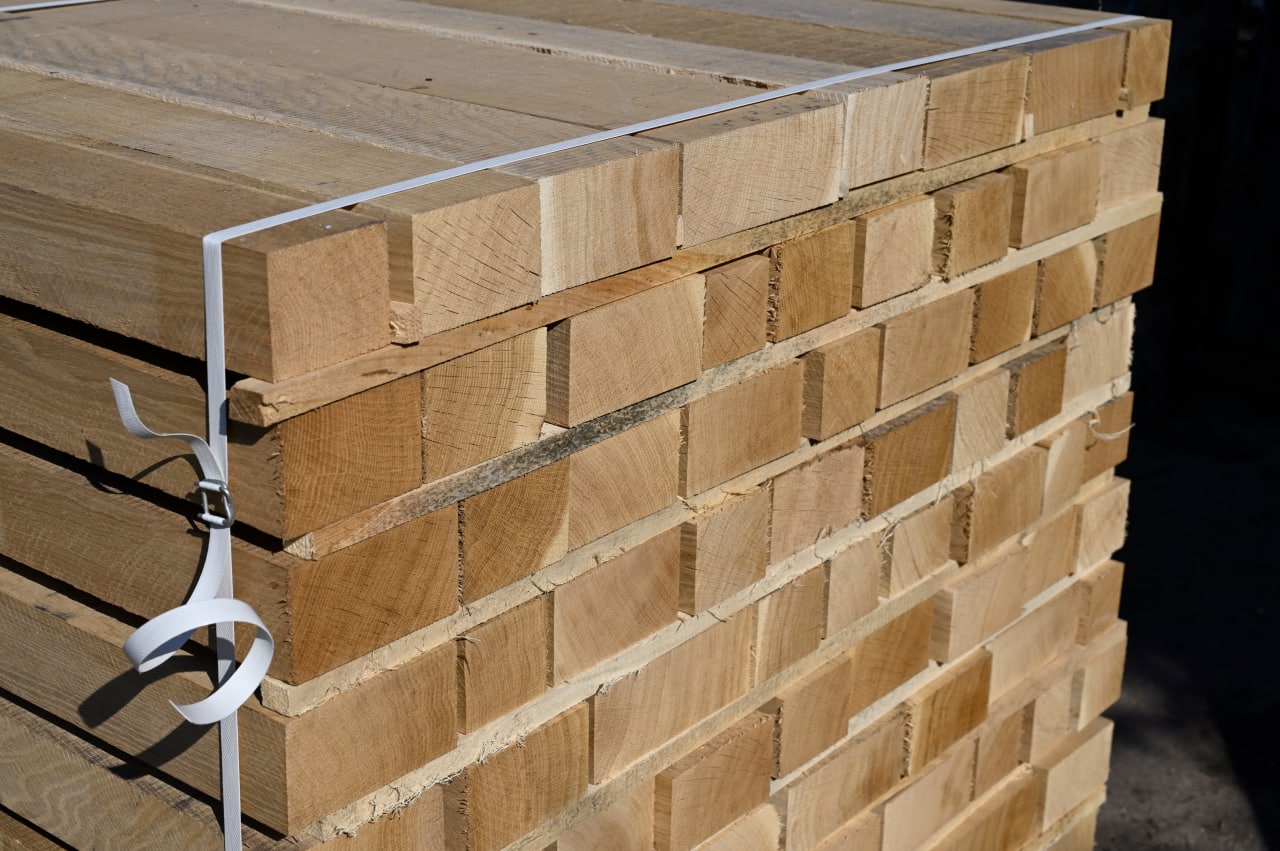
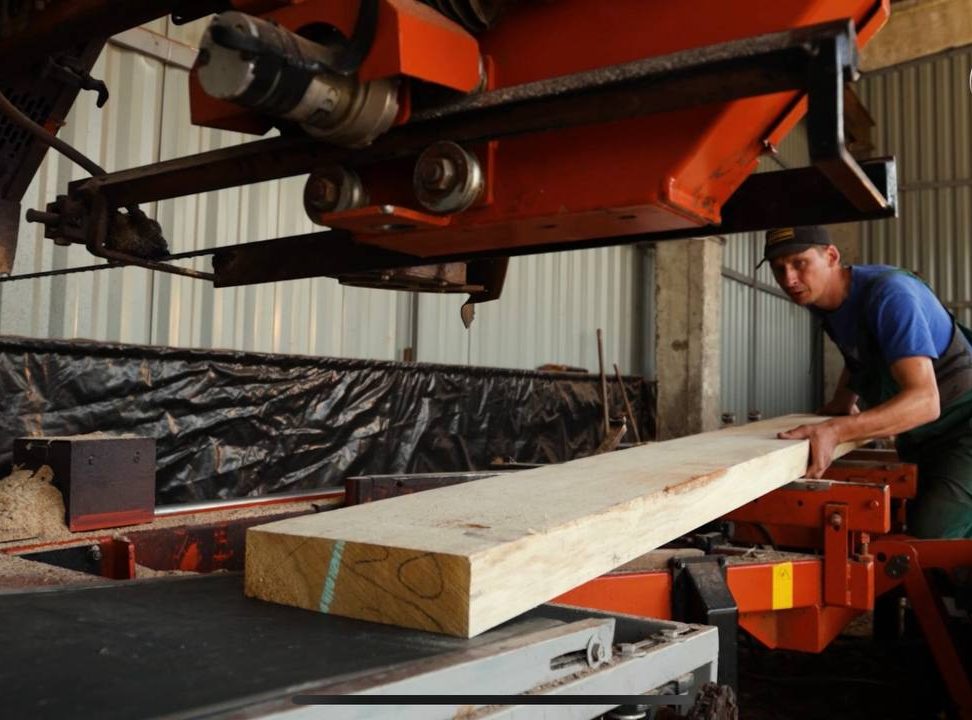
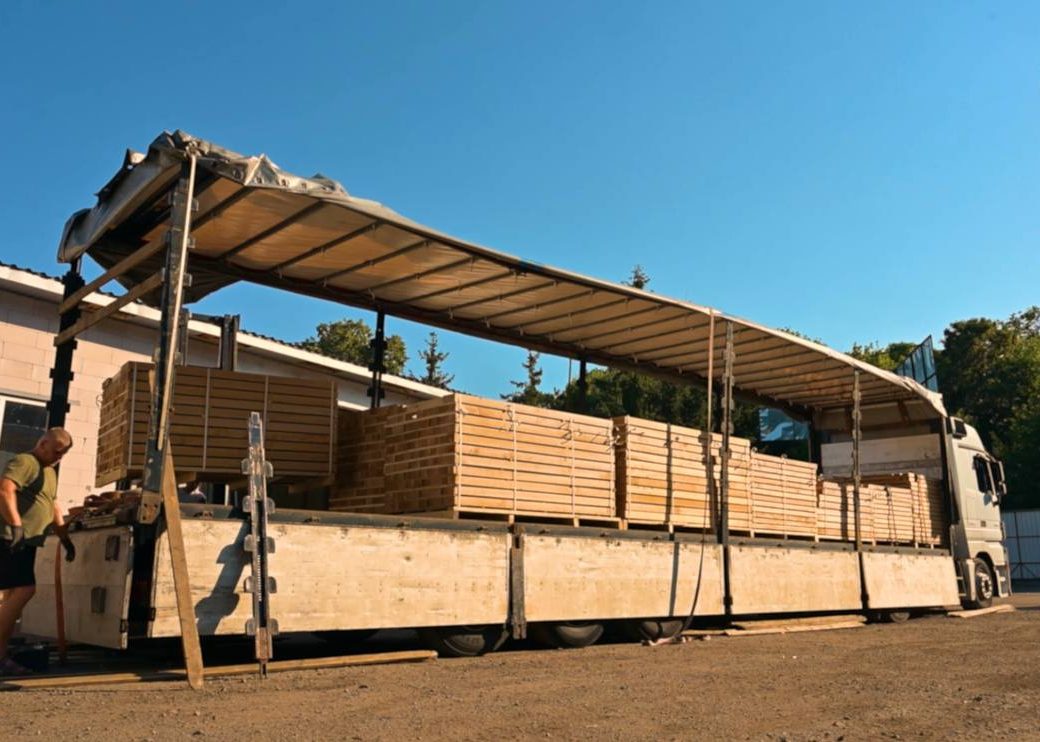
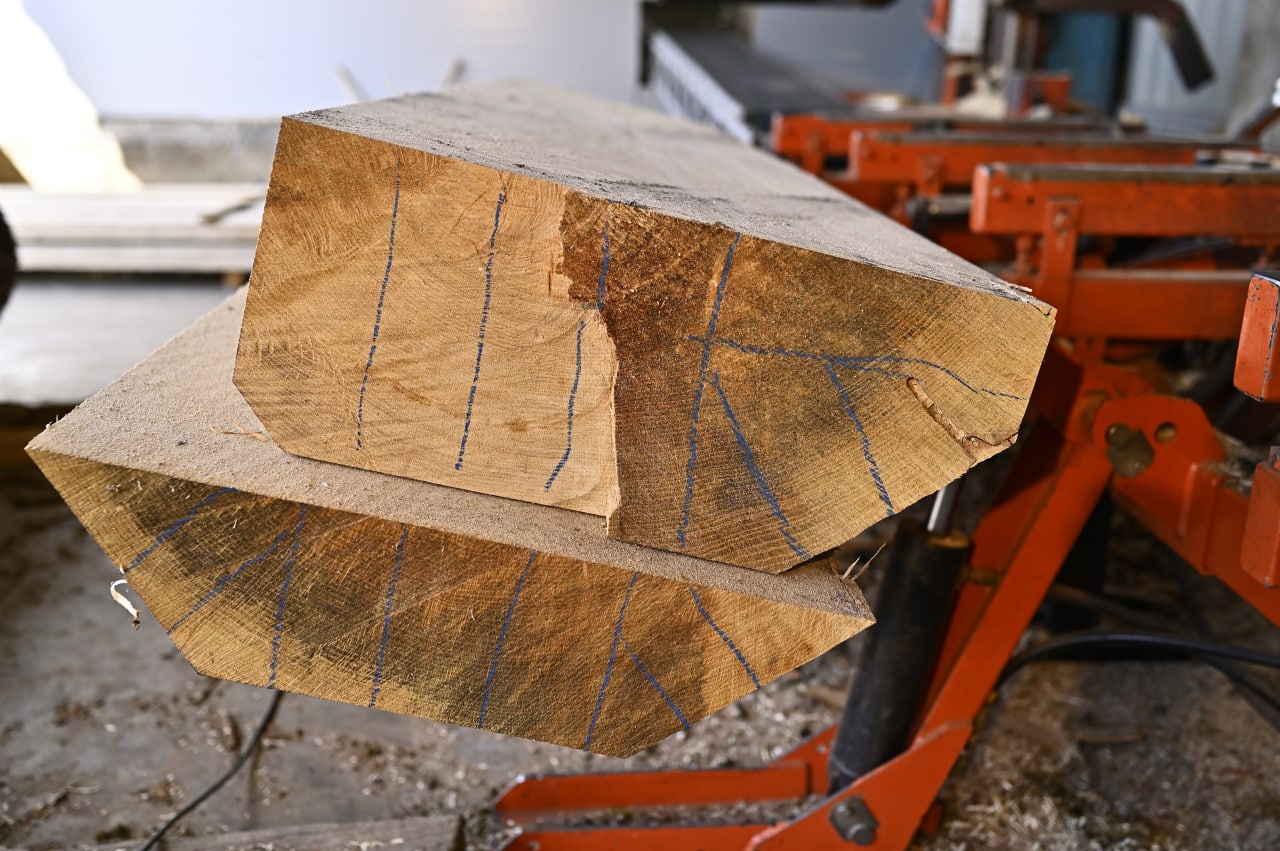
Thickness 42, 50, 54, 60, 65, 70, 80 mm (+5 mm)
Width 65-MAX
Length 1200-2800 mm (+50 mm)
The density of annual rings is not taken into account.
Sapwood is permissible up to 50% of the thickness of the rivet.
It is used for tubs with a volume of 500-5000 liters

The lamella is a technologically compound product. Wood is still an organic product and has all the characteristics of this process: drying, cracking, discoloration, moisture gain, deformation, etc. The production process requires precision, neatness and care. To save every 0.1 mm of thickness is quite a task. Each machine must meet modern requirements, and the team must be coordinated.
We have the opportunity to make lamellas in such sizes
Thickness 2.0-6.2 mm, width 62-500 mm, length 300-6000 mm
We divide the lamellae into four subgroups.
Short dimensions: Width 63-95 mm, length 300-520 mm
Average sizes: width 105-185 mm, length 620-1500 mm
Long dimensions: width 165-345 mm, length 1500-3020 mm
Extra large sizes: width 350-500 mm, length 3500-6000 mm
Products
L a m e l
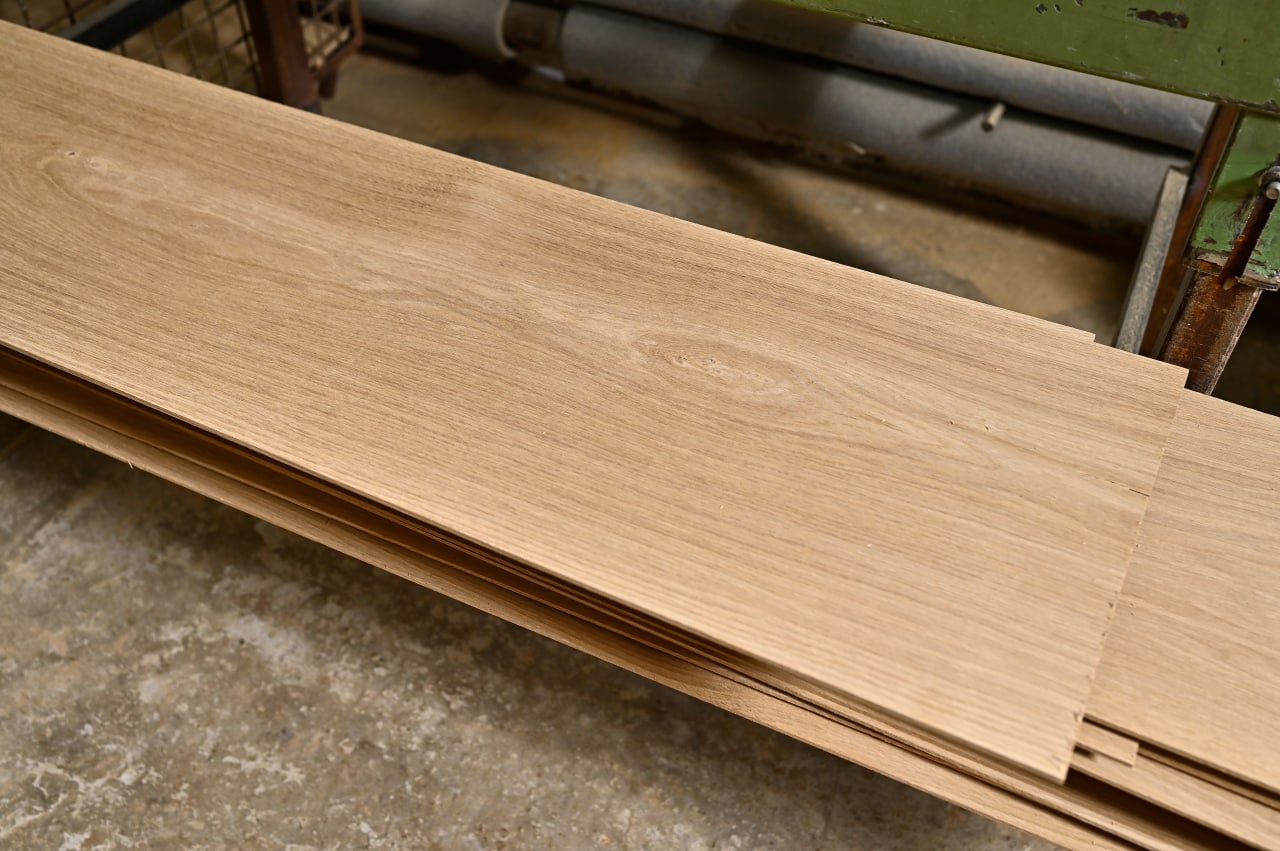
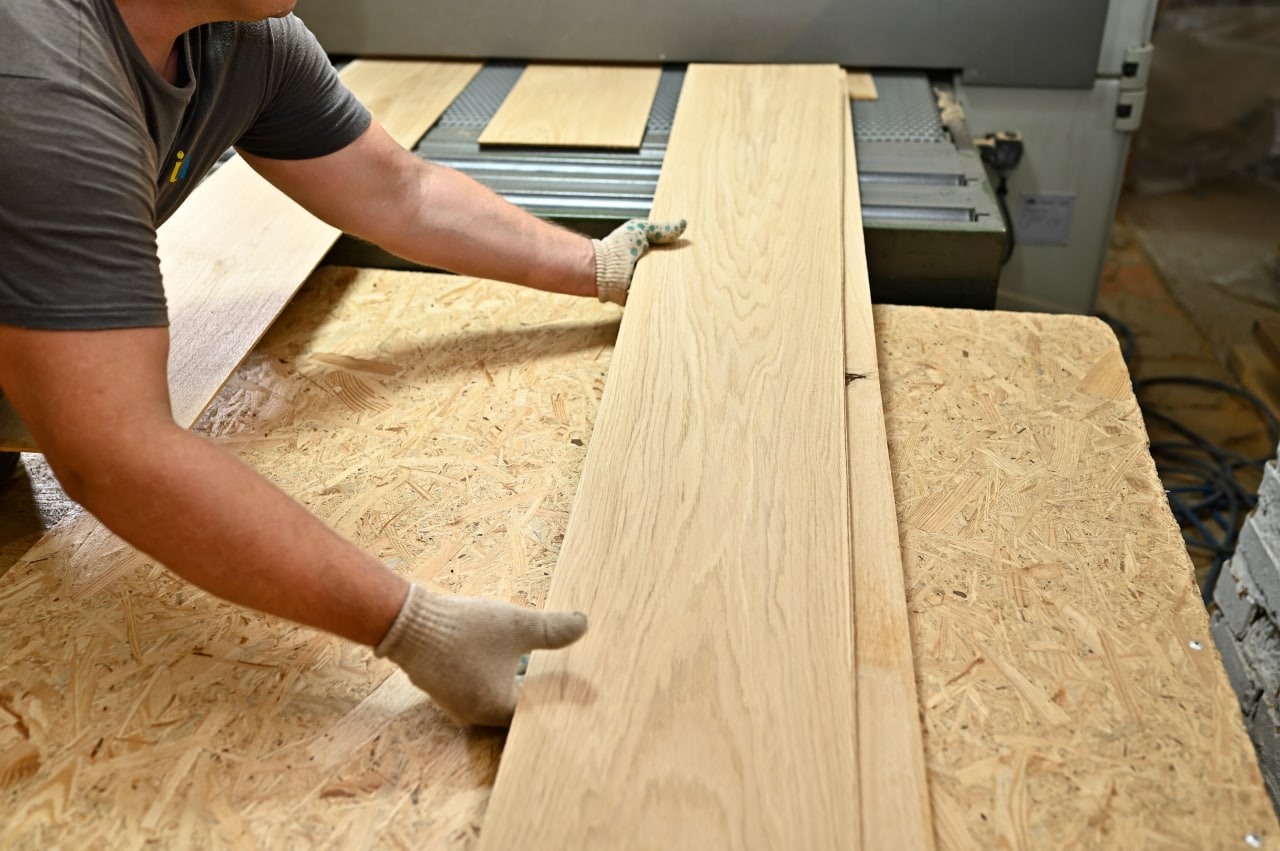
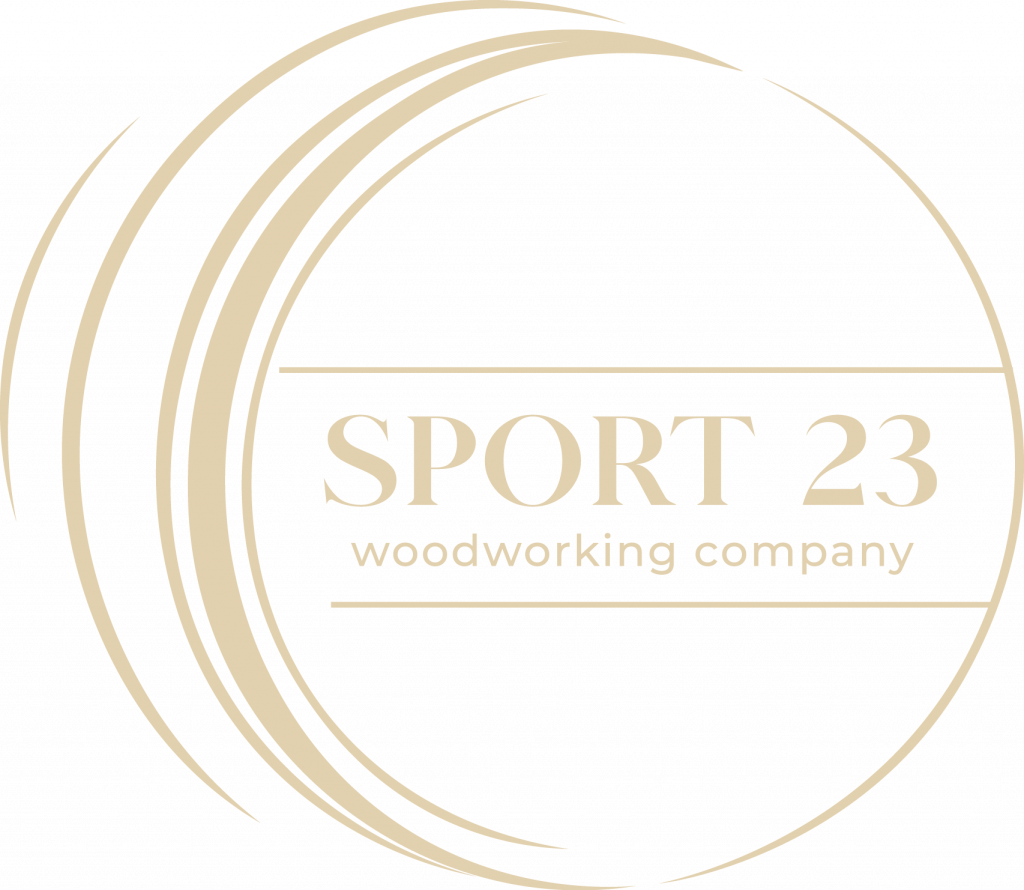
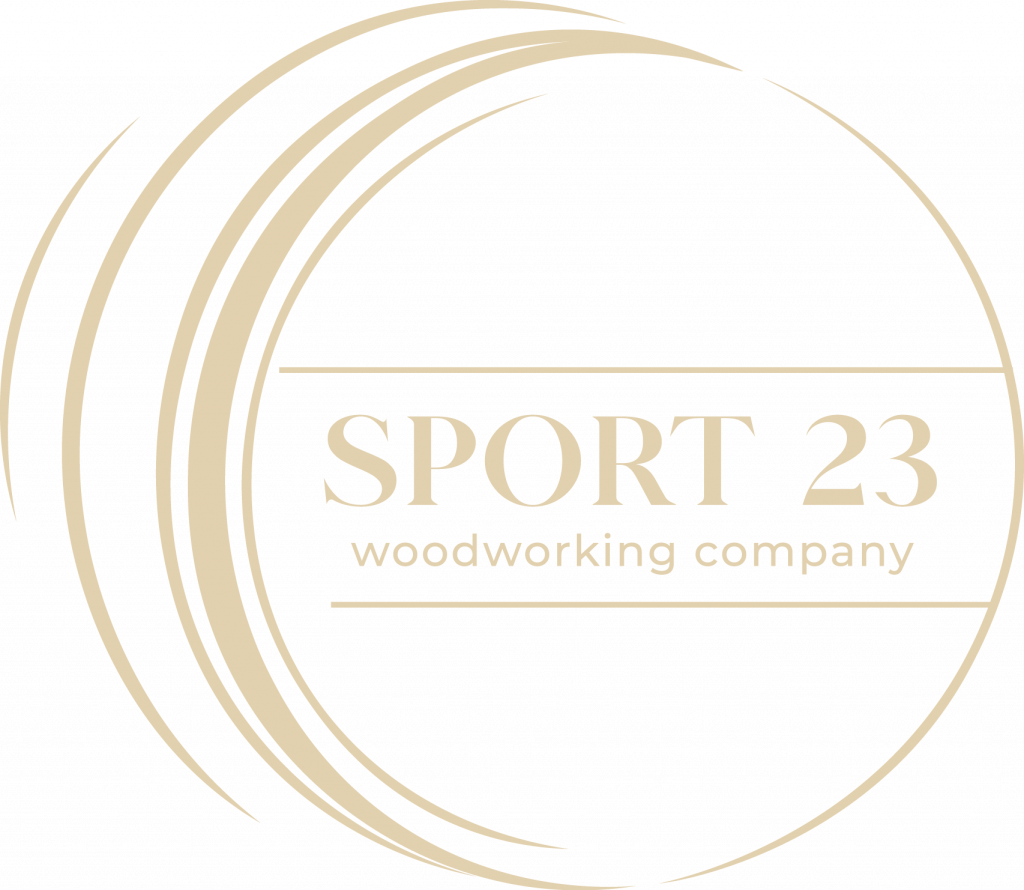
Products
F i n i s h e d p r o d u c t s
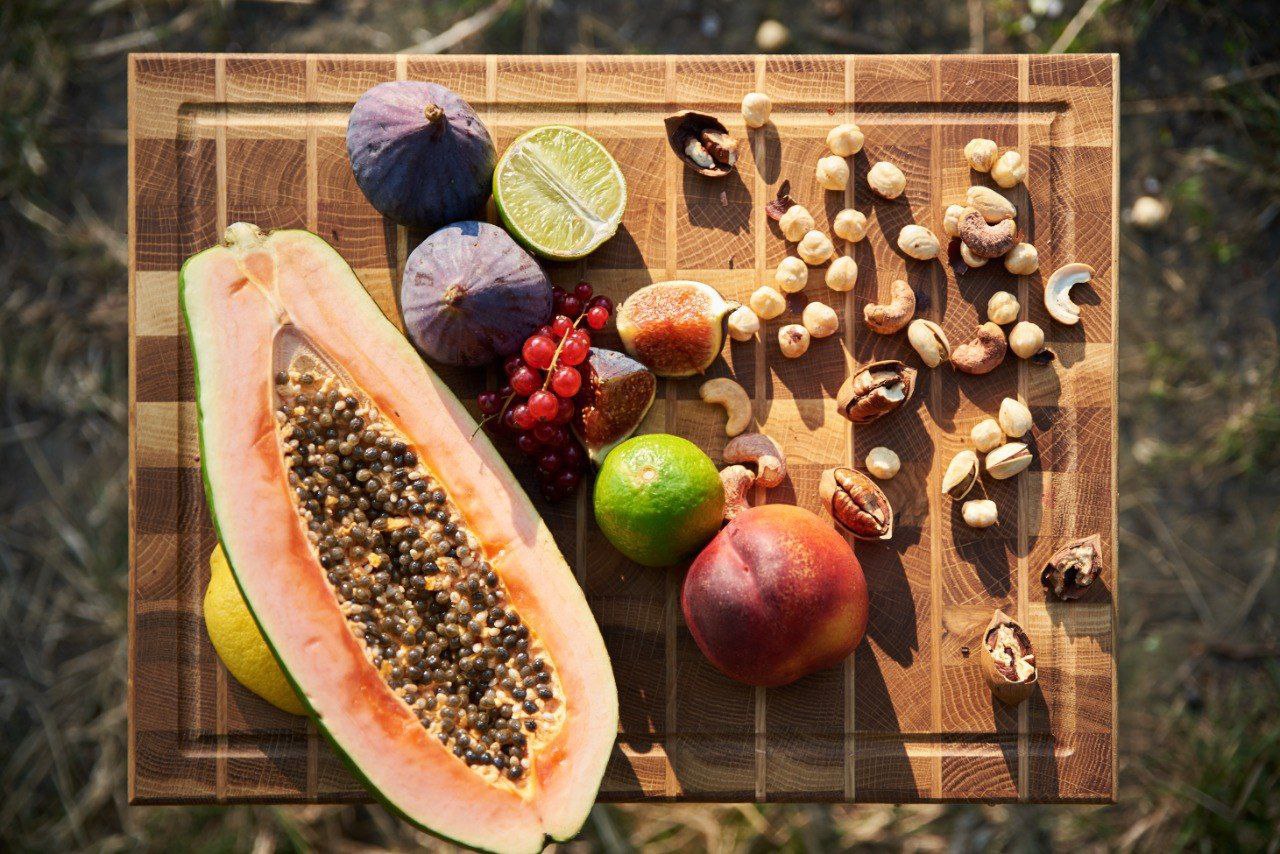
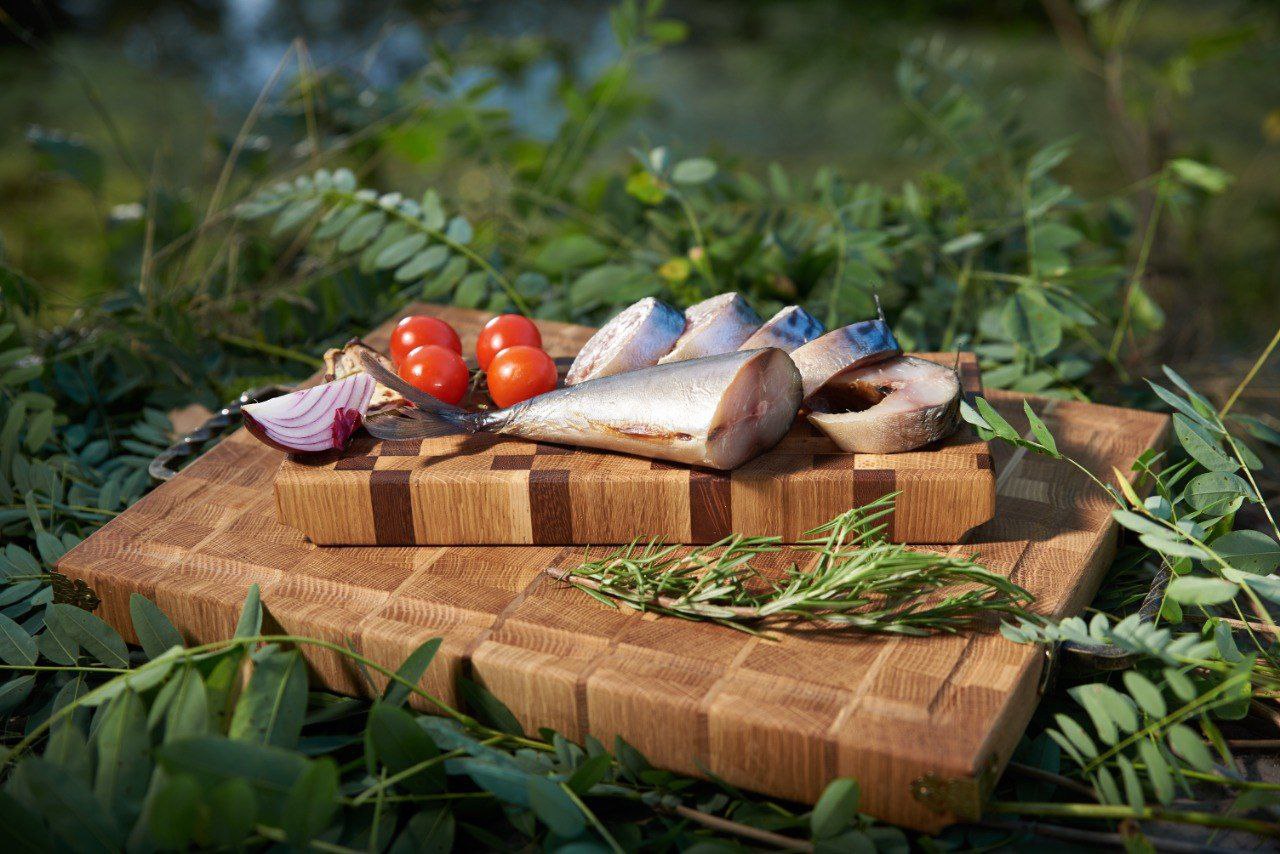
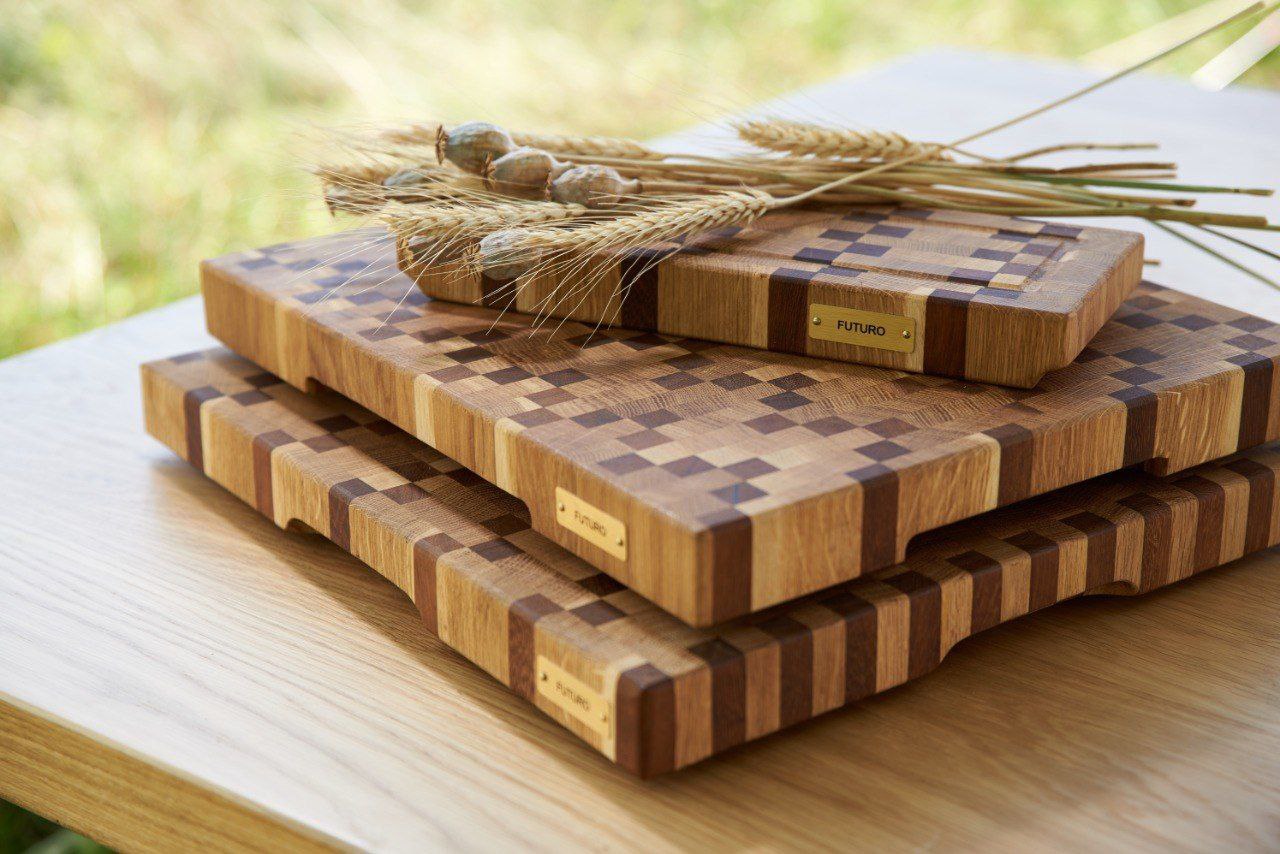
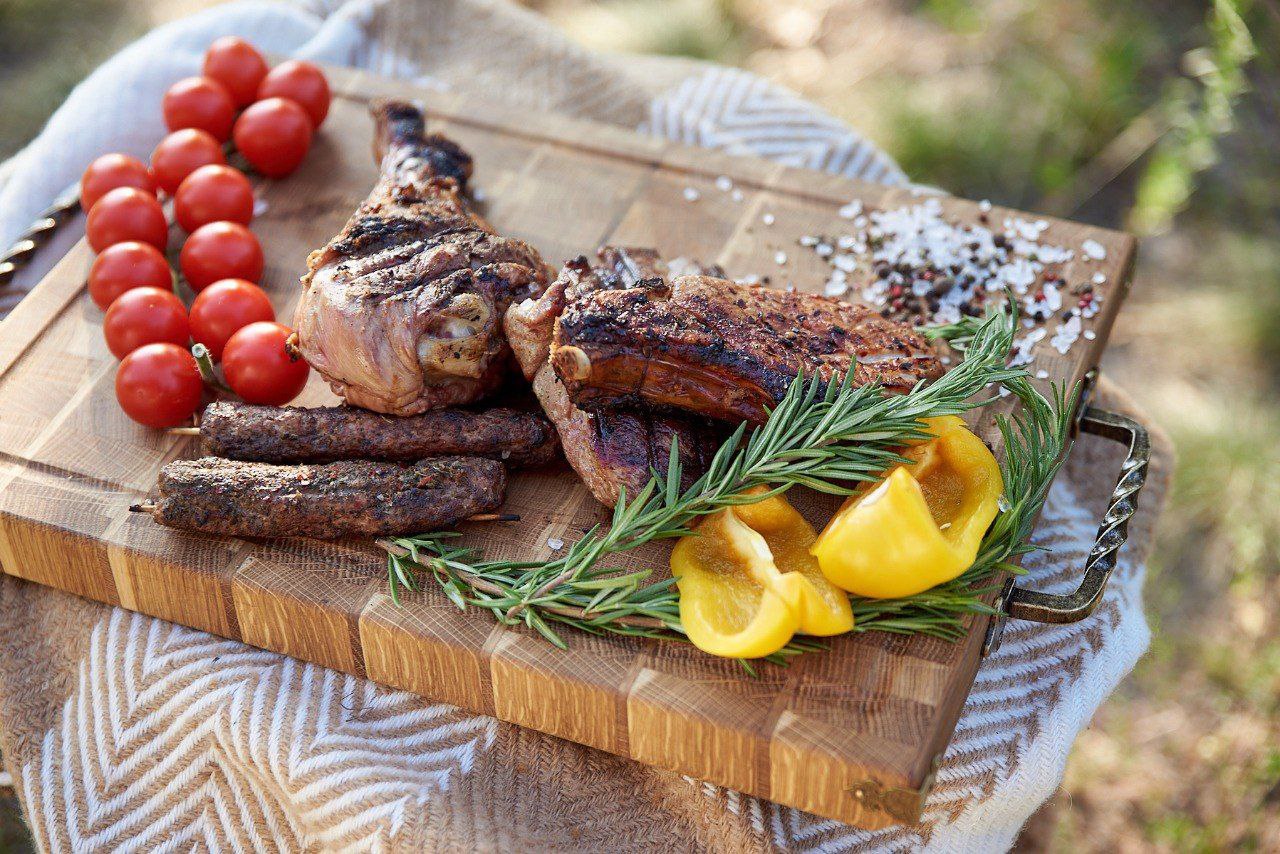
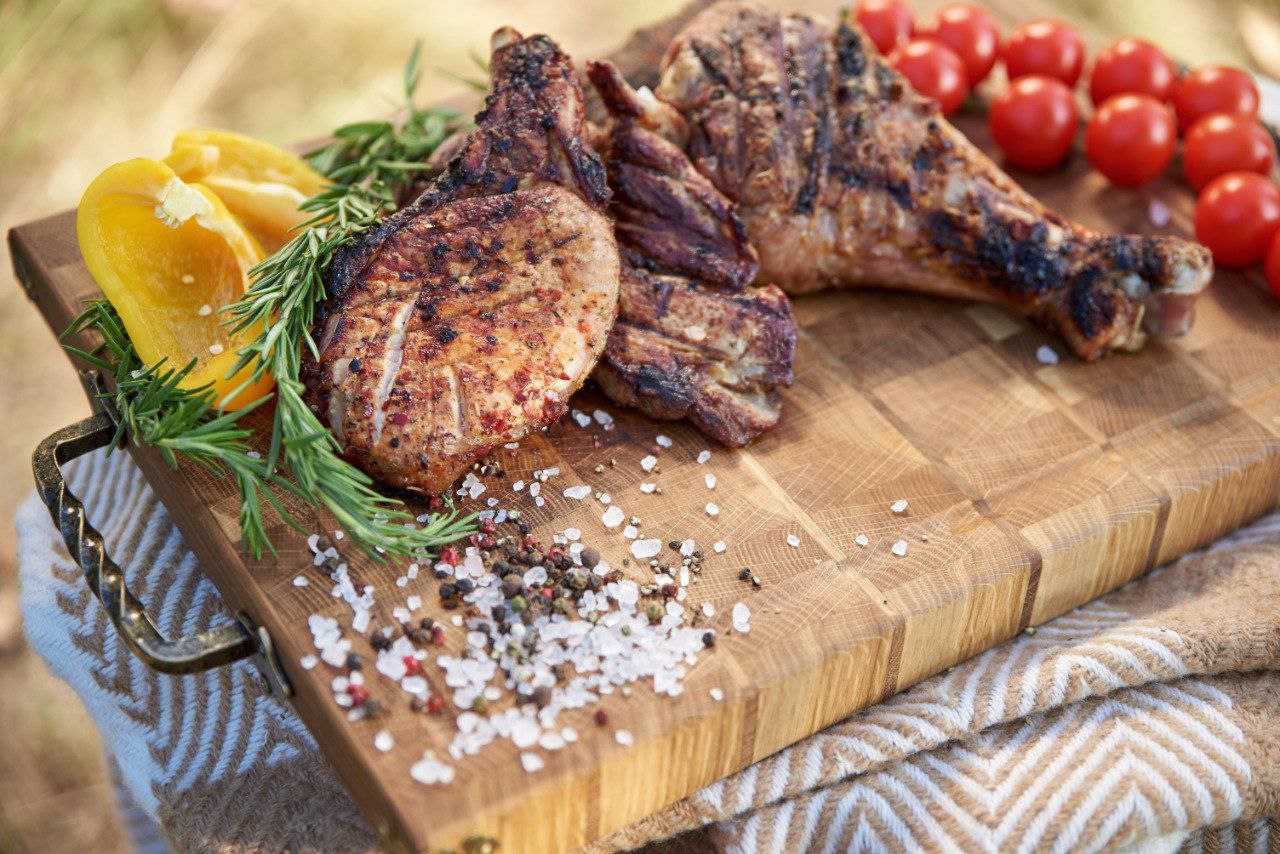
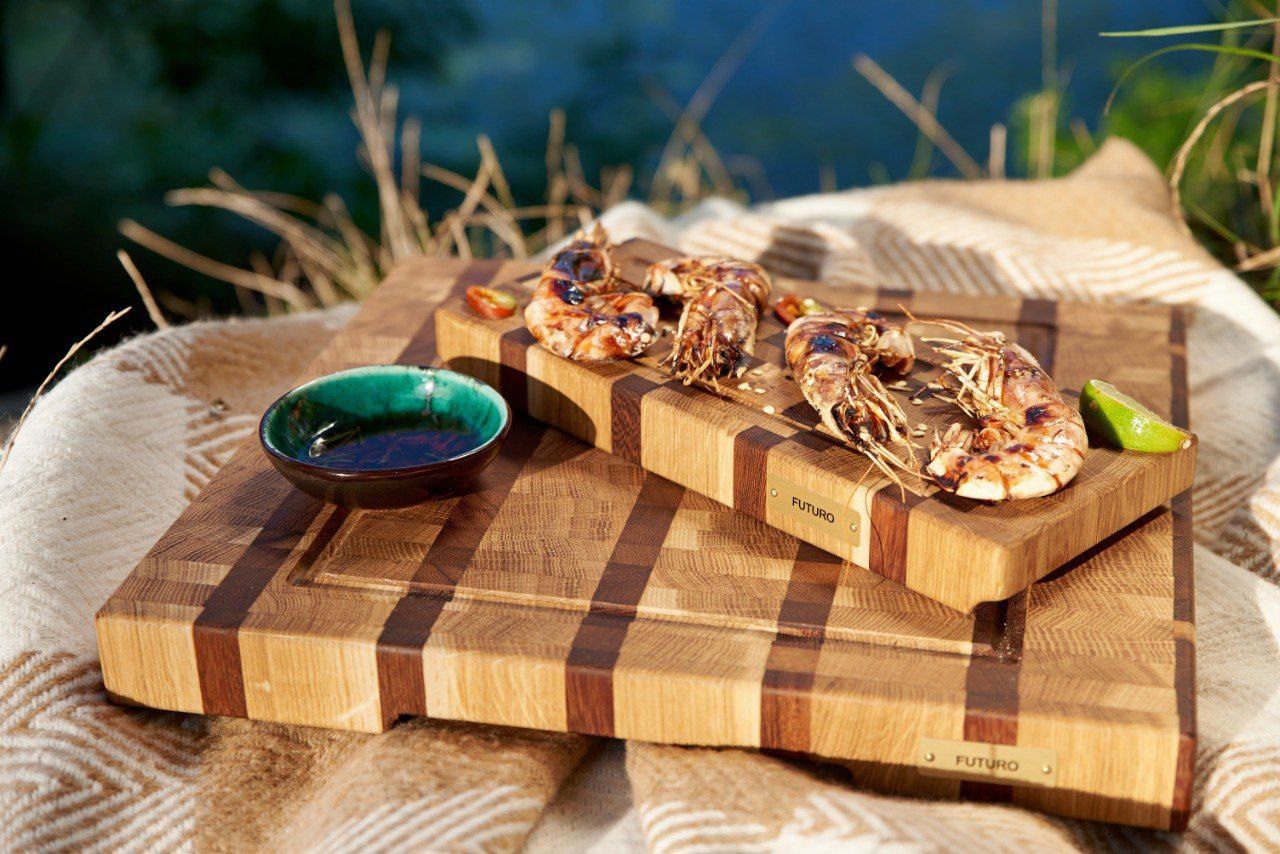
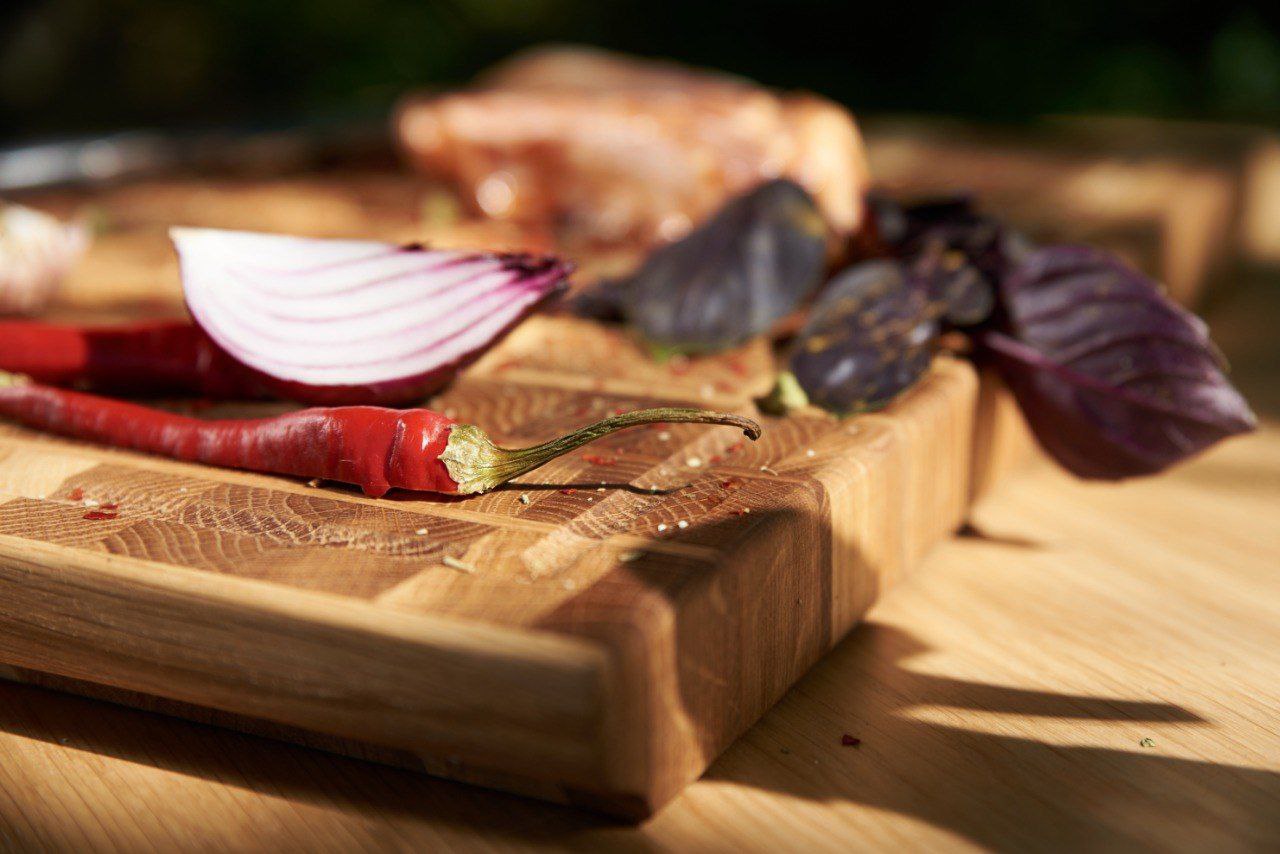
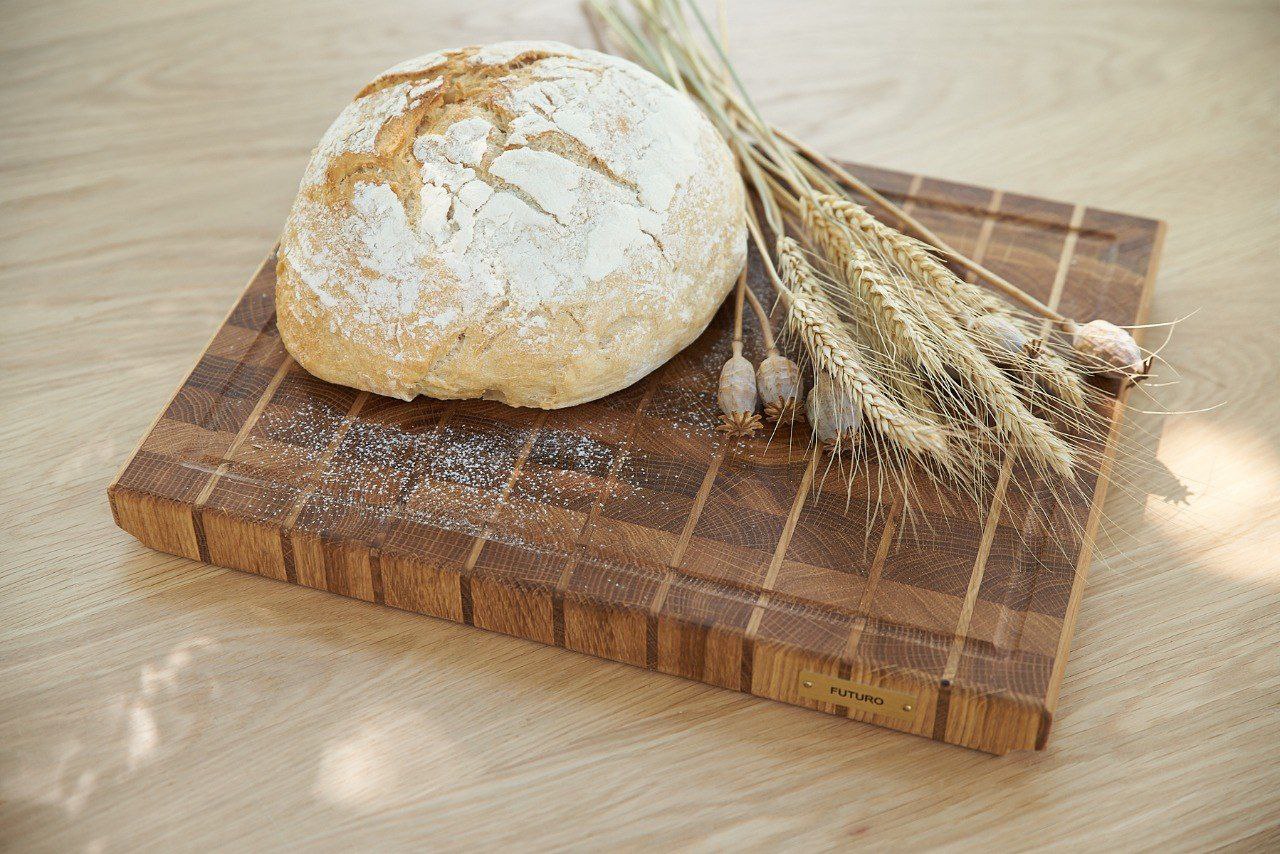
Products
E n d k i t c h e n b o a r d s m a d e o f o a k
From blanks that cannot be used in rivets or lamellas, we produce end kitchen boards, thereby maximizing the optimization of the technological process.
All boards are made using D4 glue and vaseline oil, which means that you can not be afraid to process food on these boards. If desired, the boards can be made with or without a groove, with handles, or with a laser, with any pattern burned into it.
Products
O a k c h i p s f o r d i s t i l l a t e s
Oak chips can be used to achieve various goals in the production of wine and spirits. Traditionally, toasted chips are used to adjust the aroma and taste structure, as well as to adjust the color of the drink.
Dosage:
Fermentation: 0.6 – 2 g per 1 liter or 0.33 – 1 kg per 1 ton.
Shelf life: 0.4 – 1.2 g per 1 liter, in contact with the product – 6 months. A high dosage is recommended for a short period of contact with the product or when the wine is used for blending.
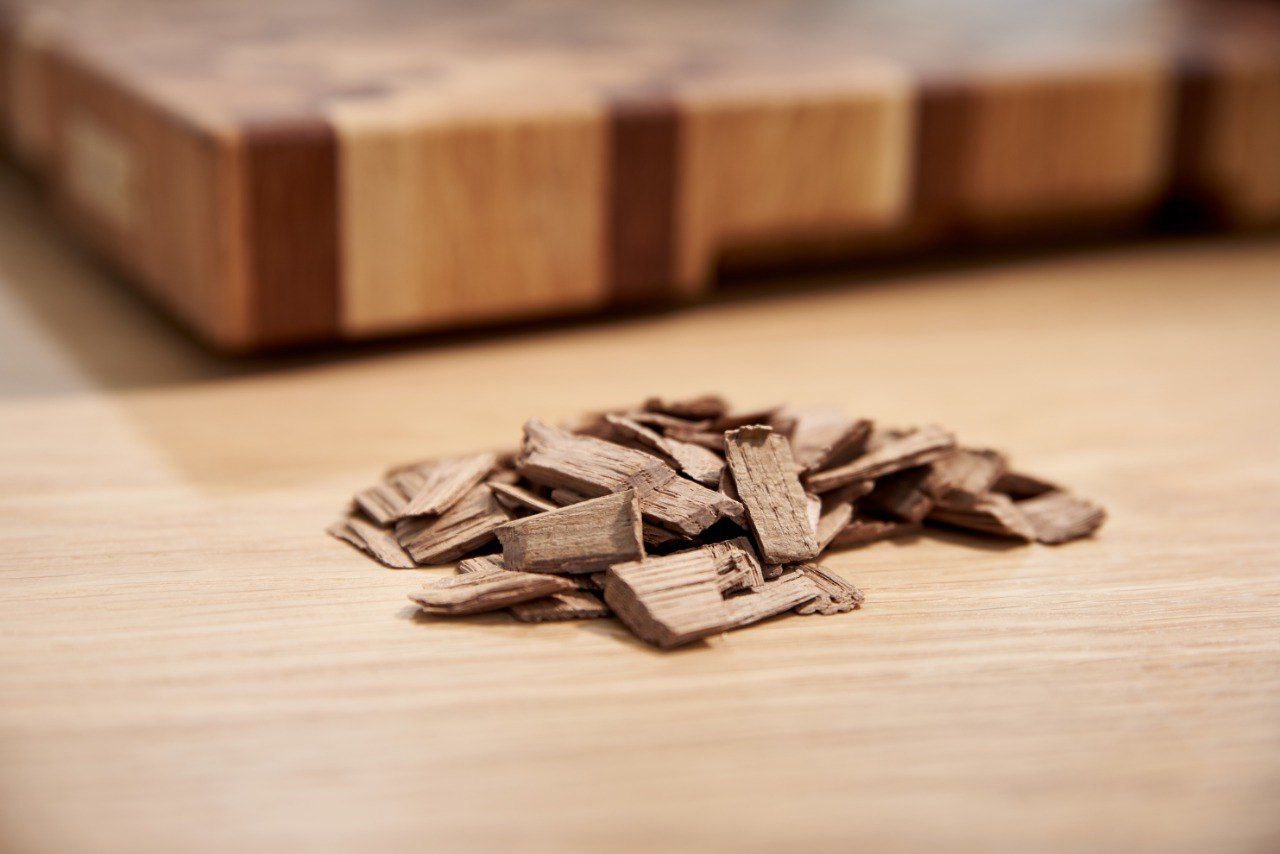
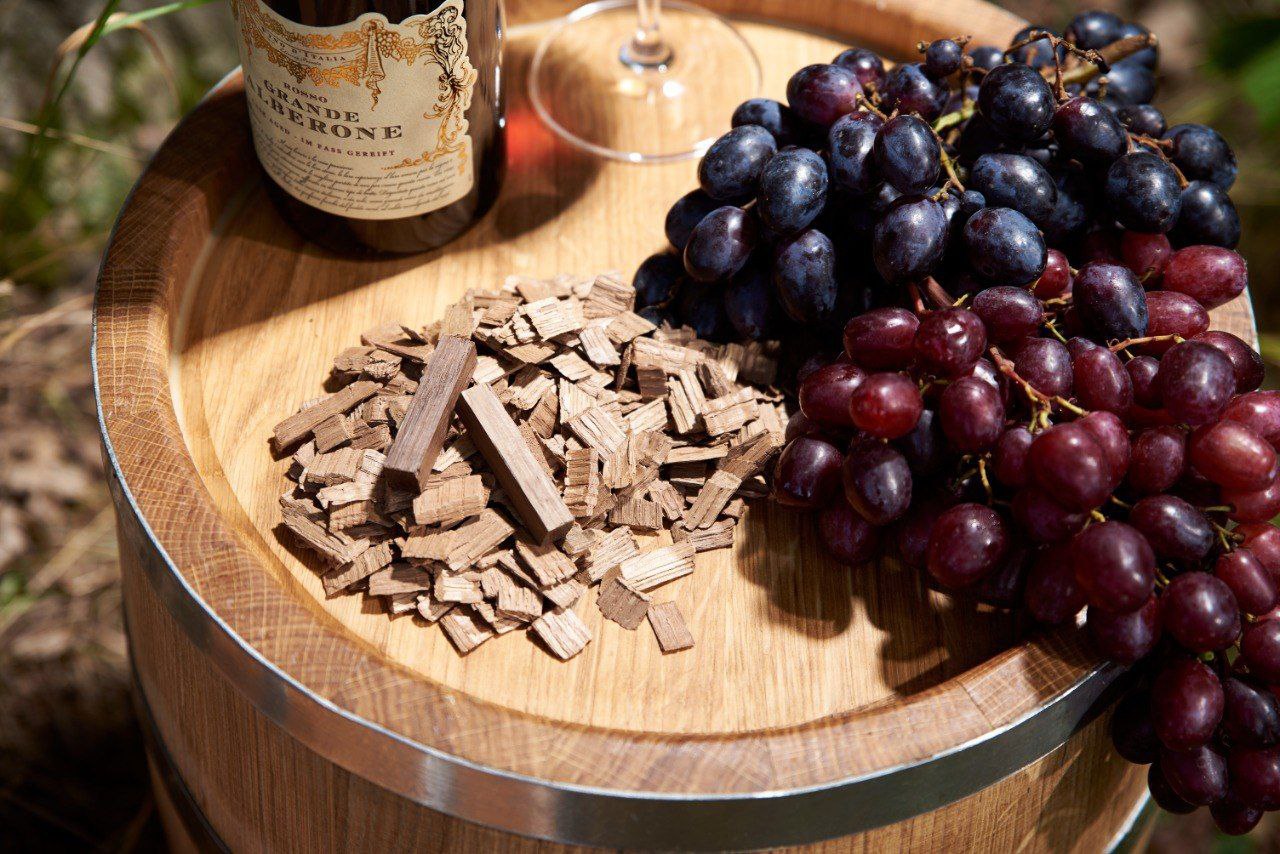
Products
C o f f e e t a b l e s
End kitchen boards made of oak.
From blanks that cannot be used in rivets or lamellas, we produce end kitchen boards, thereby optimizing the technological process as much as possible.
All boards are made using D4 glue and vaseline oil, which means that you can not be afraid to process food on these boards. If desired, the boards can be made with or without a groove, with handles, or laser burned with any pattern.
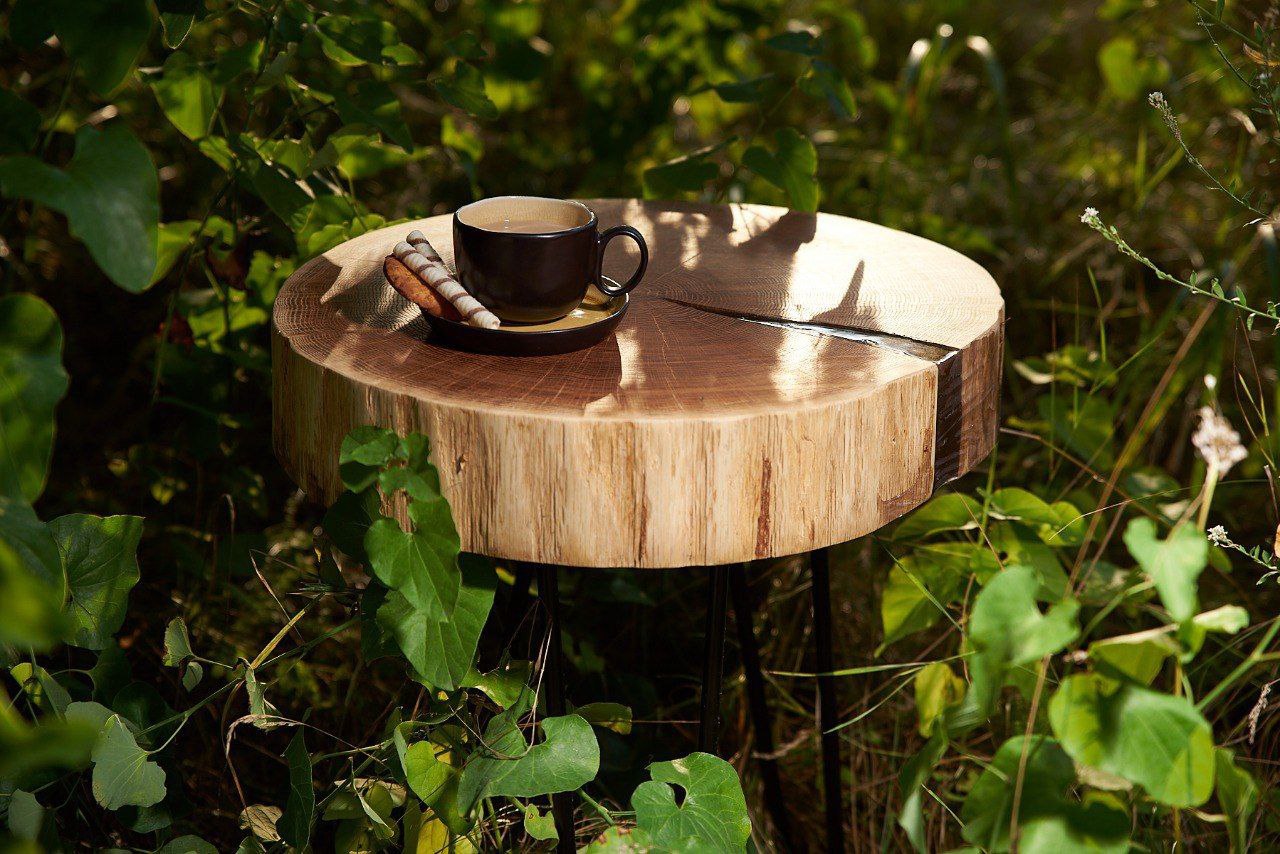
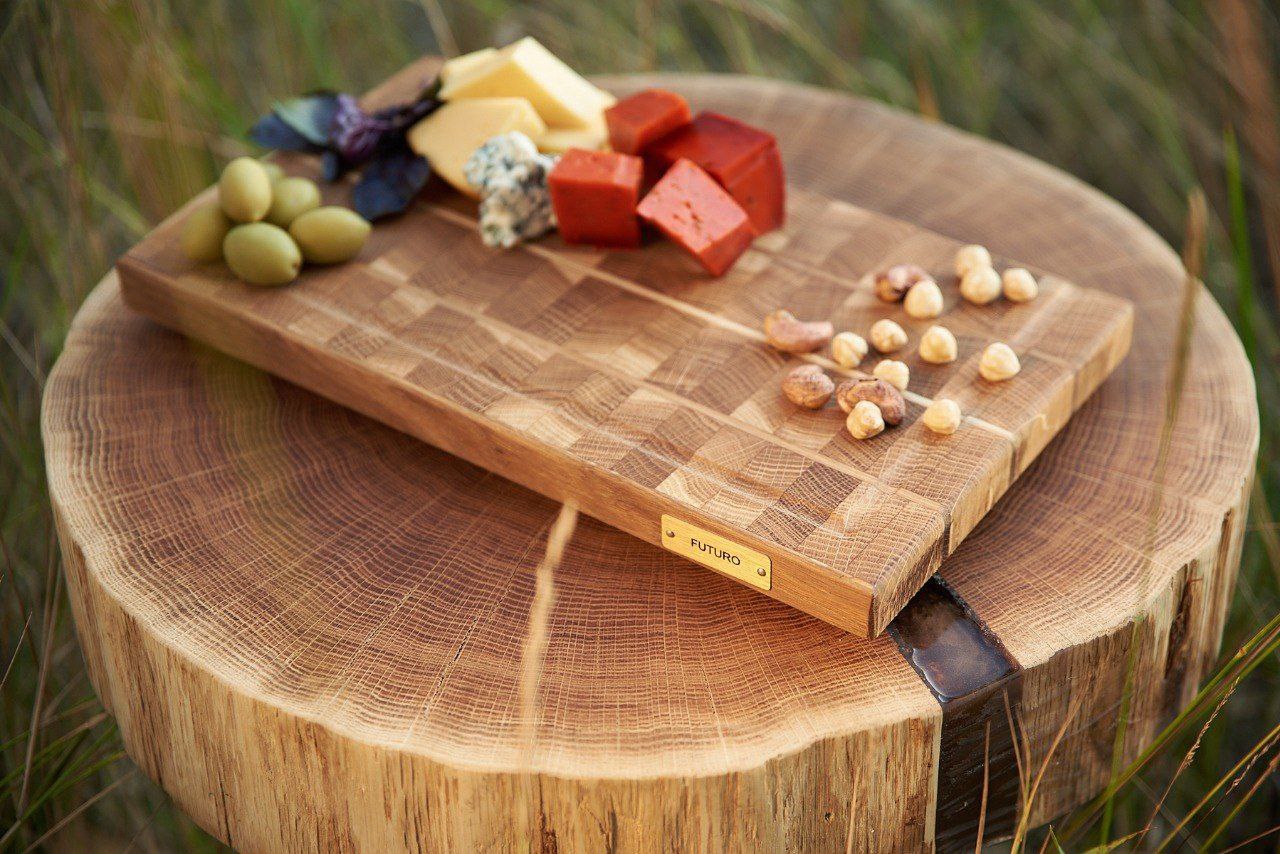
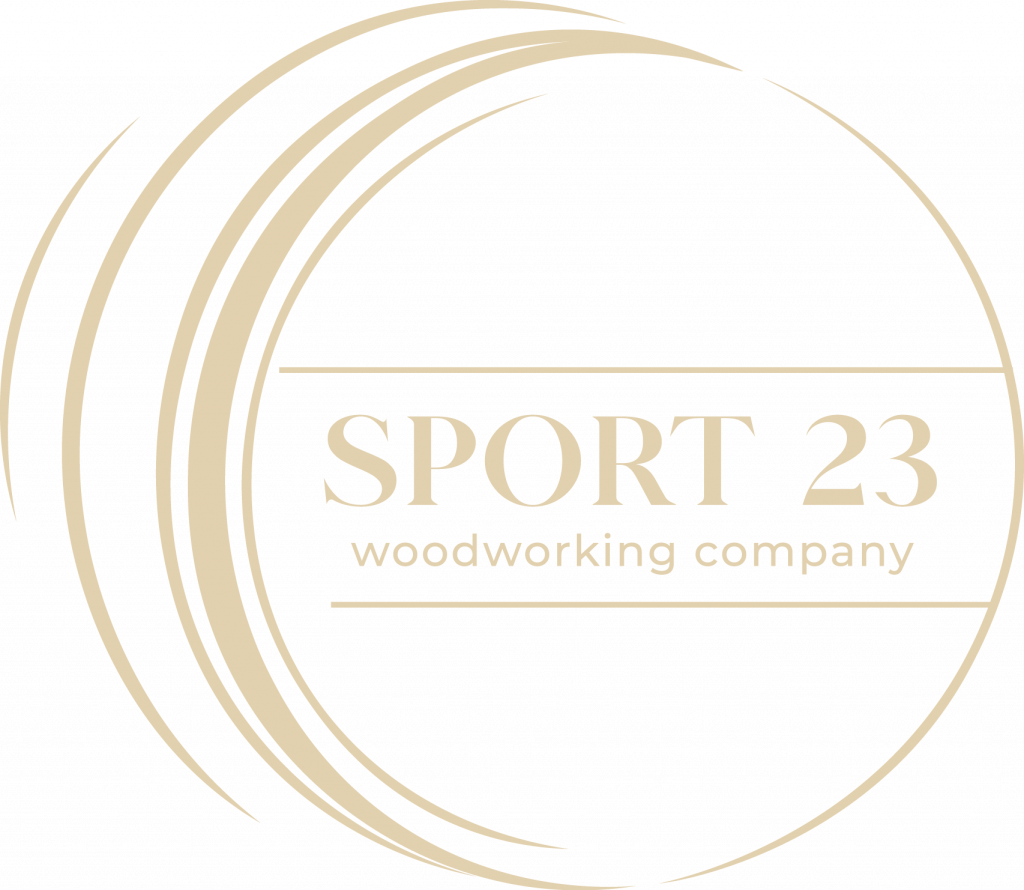
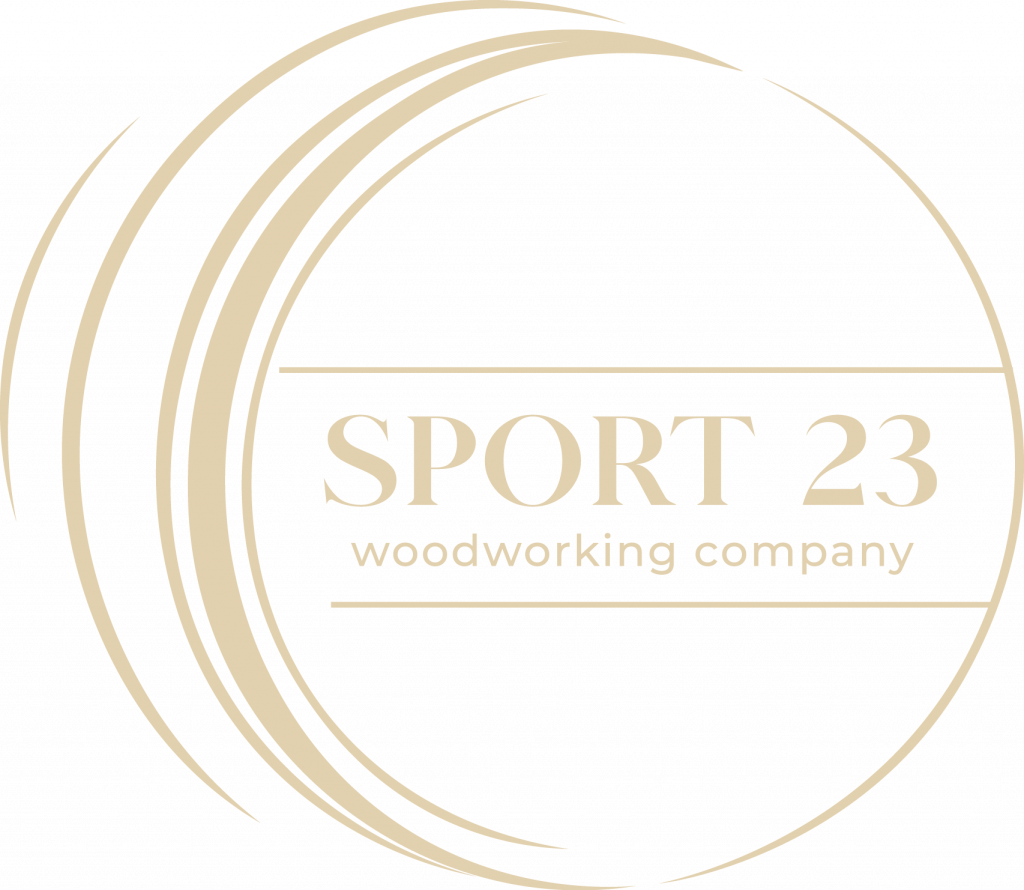
T e a m
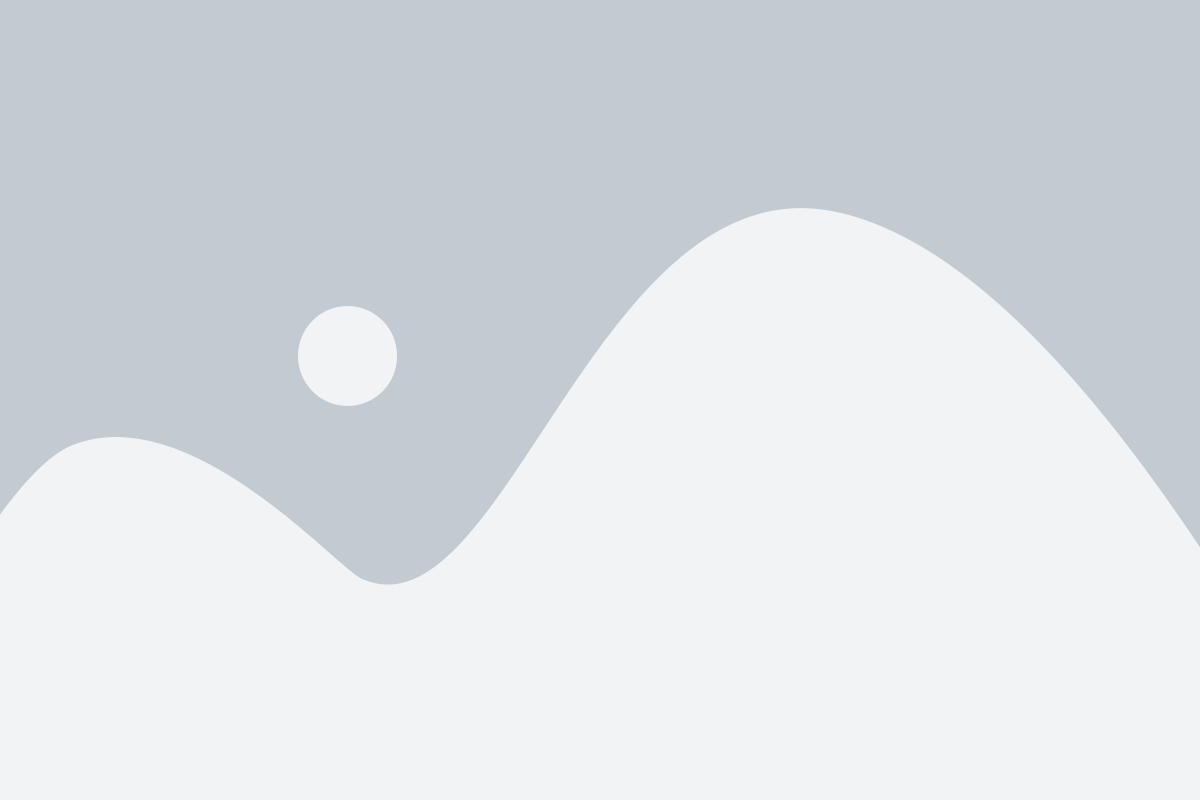
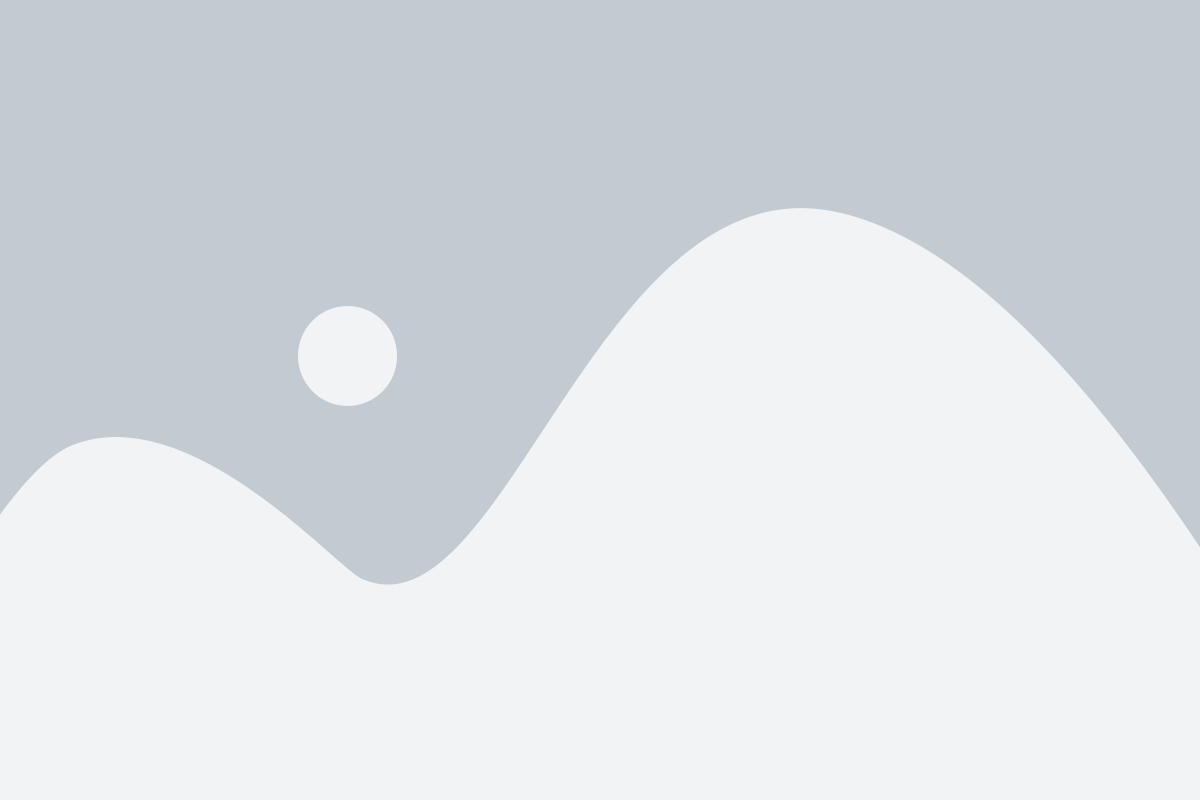